A Comprehensive Guide to HV Wiring Harnesses in Electric Vehicles
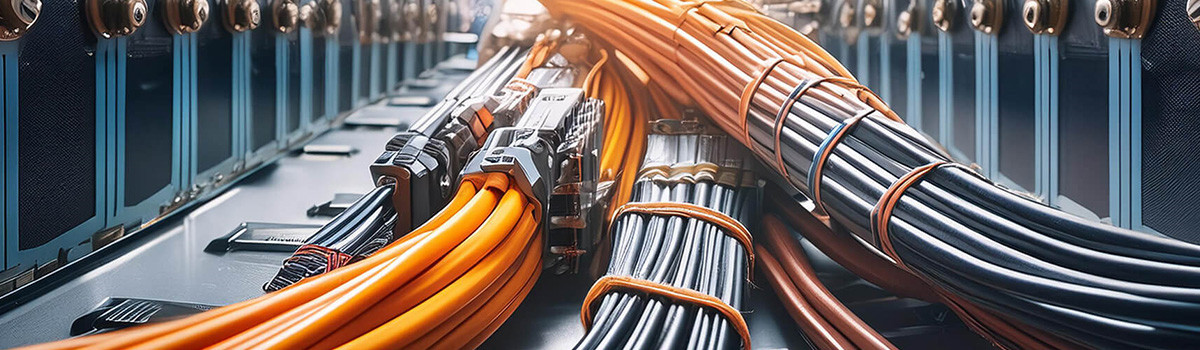
Understanding the different components of electric vehicles is essential as they have recently gained popularity. Among the key elements is the high voltage (HV) wiring harness. Below is a comprehensive guide to HV wiring harnesses in EVs, their design, functionality, safety precautions, and future trends.
1. What is a High Voltage Wiring Harness?
In an electric vehicle, the high-voltage wiring harness is the electrical conduit that carries power between the vehicle’s high-voltage battery, high-voltage motor, and various high-power systems. This harness’s functionality significantly differs from conventional vehicle harnesses because most conventional vehicles operate between 12V and 48V. In contrast, electric cars work between 300V and 1,000V. This creates challenges for the automobile industry regarding designing such products for optimal performance.
2. Functionality and Key Components
The HV wiring harness is the main artery of power distribution in EVs. It connects essential components like the battery, electric motor, onboard charger, and inverter. Here’s how each component interacts within the EV system:
Table: Voltage and Current Ranges in Key EV Components
System Component | Voltage Range | Current Range |
---|---|---|
Battery Pack | 400V – 800V | 100A – 300A |
Electric Motor | 400V – 800V | 50A – 300A |
Onboard Charger | 240V – 500V | 20A – 60A |
Inverter | 400V – 800V | / |
This high-voltage wiring enables EVs to efficiently manage and deliver power, ensuring smooth acceleration, battery charging, and overall energy management.
3. Materials and Design Requirements
High-voltage wiring harnesses must withstand various environmental conditions, including extreme temperatures, vibrations, and chemical exposure. The insulation materials used for these harnesses are critical to their durability and safety.
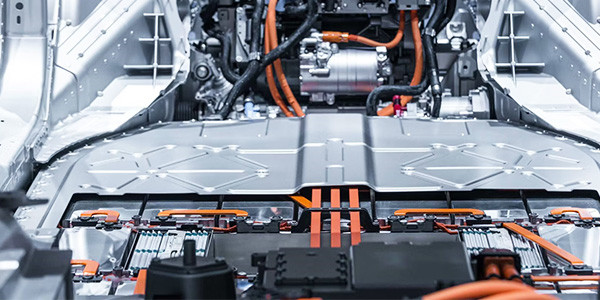
Table: Common Insulation Materials in HV Wiring Harnesses
Insulation Material | Temperature Resistance | Mechanical Strength | Chemical Resistance |
---|---|---|---|
Cross-linked Polyethylene (XLPE) | -40°C to 125°C | High | Excellent |
Silicone Rubber | -60°C to 200°C | Moderate | Excellent |
Polyvinyl Chloride (PVC) | -40°C to 105°C | Low | Good |
These materials help protect the conductors from short circuits, electrical faults, and mechanical wear and tear.
4. Safety and Regulations
Safety is of the utmost importance when dealing with high-voltage components. Various international standards ensure that high-voltage wiring harnesses are designed and tested to meet rigorous safety protocols.
Key Safety Standards for HV Wiring Harnesses
Standard | Description |
---|---|
ISO 26262 | Functional safety standard for road vehicles. |
IEC 62196 | Standards for connectors and charging infrastructure. |
ISO 6722 | Electrical insulation standards for road vehicles. |
These regulations help minimize the risks of electrical hazards, ensuring the long-term safety of electric vehicles on the road.
5. Common Issues and Solutions
Even with the best designs, high-voltage wiring harnesses can encounter issues. Below are some common problems and solutions:
- Overheating: Ensure that the cables are rated for the current they need to carry and that enough thermal management is provided.
- Insulation Wear: Periodic inspections and good-quality insulation materials can avoid premature degradation.
- Corrosion: Proper sealing and waterproofing methods will keep the moisture and chemicals away from corrosion.
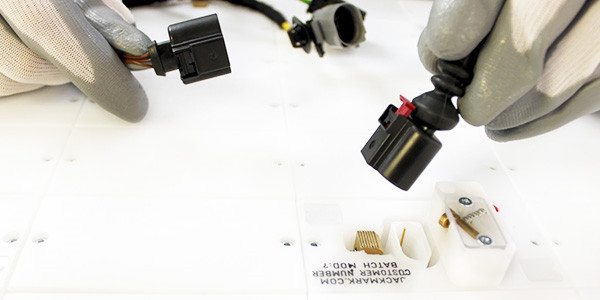
6. Real-World Cases
Case Study 1: Tesla Model 3
The wiring harness for high voltage in the Tesla Model 3 is an innovative design that connects different cables to achieve a perfect connection between the battery pack and the electric motor. This is possible using the latest materials and Tesla’s very accurate engineering. Indeed, this harness will not only deliver power but also do so with minimum weight. Because Tesla optimized this design, there was an improvement in the range for which the vehicle would operate, as well as the general performance. This is just excellence in design that can drive tremendous results for electric vehicle technology.
Case Study 2: BMW i3
In the BMW i3, the high-voltage wiring harness includes a state-of-the-art battery management system that monitors the status of the battery in real-time. The key aspect of this design is the lightweight approach, high strength, low-weight material used to meet the efficiency needs of the vehicle. BMW has also initiated a modular design for its wiring harness to make it easily maintained and replaced when required. Such thoughtfulness does not just increase the maintainability of the vehicle but also keeps it, leading to electric mobility.
7. Future Trends in High Voltage Wiring Harnesses
The development of electric vehicles raises increasing demands for high-voltage wiring harnesses. Consequently, manufacturers would focus on making the system lightweight, efficient, and environmentally stress-resistant.
Innovations include new composite materials for insulation, increased integration of sensors for real-time monitoring, and efforts to reduce the weight and bulk of the wiring systems to improve vehicle efficiency.