Automotive Wiring Harness Manufacturers
Comprehensive Guide to Automotive Wiring Harness Manufacturers
Comprehensive Guide to Automotive Wiring Harness Manufacturers
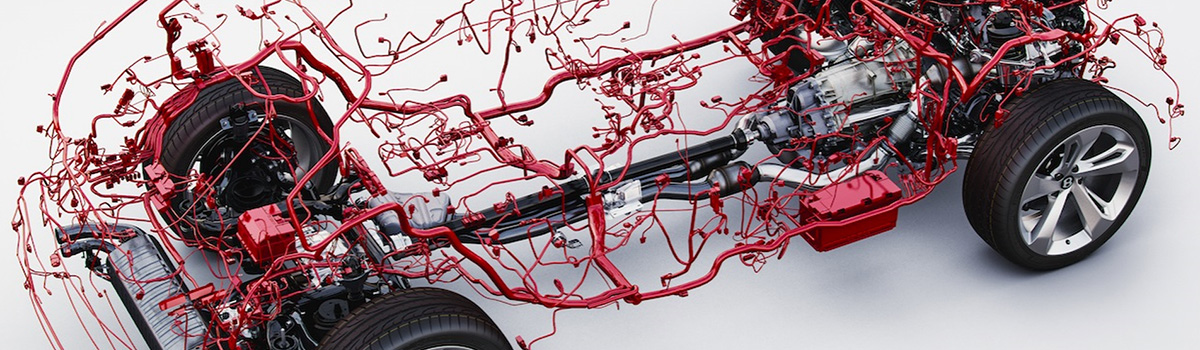
In the intricate world of automotive engineering, few components are as essential yet often overlooked as the wiring harness. This complex assembly of wires, connectors, and terminals serves as the central nervous system of a vehicle, transmitting power and data to every corner of the car. From the engine’s roar to the gentle glow of dashboard lights, the wiring harness makes it all possible. At the heart of this critical system are automotive wiring harness manufacturers, the unsung heroes who design, produce, and innovate these vital components. Let’s delves deep into their world, exploring their roles, challenges, innovations, and the future trends shaping this dynamic industry.
Table of Contents
ToggleWhat is a Wiring Harness?
An automotive wiring harness is an organized set of wires, connectors, and terminals bundled together to provide electrical connections throughout a vehicle. Custom-designed for each make and model, these harnesses ensure that every component—from the smallest sensor to the most power-hungry system—receives the electricity and signals it needs to function. Think of it as the circulatory and nervous system of a car, delivering power and information seamlessly.
Why Are Wiring Harnesses Important?
The significance of wiring harnesses in modern vehicles cannot be overstated. They support a wide range of functions, including:
- Power Distribution: Delivering electricity from the battery to various systems.
- Signal Transmission: Carrying data between sensors, control units, and actuators.
- Safety Features: Enabling critical systems like airbags and anti-lock brakes.
- Comfort and Convenience: Powering infotainment systems, climate control, and more.
As cars have evolved from simple mechanical machines to high-tech marvels with features like autonomous driving and electric powertrains, the complexity of wiring harnesses has increased exponentially. Today, the average car contains miles of wiring, with luxury vehicles boasting over 1,500 individual wires. These harnesses are engineered to withstand extreme temperatures, vibrations, and environmental conditions while maintaining optimal performance.
The Evolution of Wiring Harnesses
In the early days of motoring, automotive wiring was rudimentary—simple, individual wires connected basic electrical components like headlights and starters. As vehicles incorporated more features, the need for a more organized system became apparent. The introduction of the wiring harness revolutionized automotive electrical systems by bundling wires together and routing them through protective sheaths. This innovation reduced the risk of short circuits, improved reliability, and simplified assembly processes, paving the way for rapid advancements in automotive technology.
Now, as we stand on the brink of a new era—with electric vehicles (EVs), autonomous driving, and connected cars becoming mainstream—the role of automotive wiring harness manufacturers is more critical than ever. This article will explore their multifaceted contributions, the challenges they face, and the innovations driving the future of this industry.
The Role of Automotive Wiring Harness Manufacturers
Automotive wiring harness manufacturers are specialized companies that design, develop, and produce these complex electrical systems for vehicle manufacturers (OEMs) and aftermarket suppliers. Their work requires a blend of engineering expertise, manufacturing prowess, and logistical acumen. Here’s a closer look at their key responsibilities:
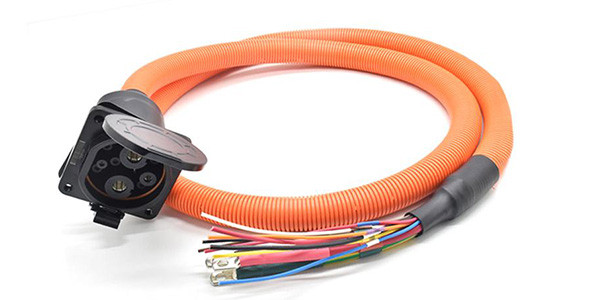
1. Design and Development
The journey of a wiring harness begins with design. Manufacturers collaborate closely with OEMs to create custom harnesses tailored to each vehicle’s electrical architecture. This process involves:
- Translating technical specifications into detailed wiring diagrams.
- Selecting appropriate wires, connectors, and protective materials.
- Optimizing layouts for efficient routing and minimal weight.
- Ensuring compliance with industry standards and regulations.
Advanced computer-aided design (CAD) software and simulation tools allow manufacturers to create virtual models and test performance under various conditions before production begins.
2. Production Processes
Once the design is finalized, manufacturers translate it into a physical product through a series of intricate steps:
- Wire Preparation: Cutting wires to precise lengths, stripping insulation, and crimping terminals.
- Harness Assembly: Laying out wires, bundling them with tapes or conduits, and installing connectors.
- Quality Control: Conducting visual inspections, continuity tests, high-voltage tests, and environmental stress tests.
While automation—such as robotic wire cutting and crimping—has improved efficiency, the complexity of harness assembly often requires skilled technicians for tasks machines can’t yet replicate.
3. Supply Chain Management
Wiring harness production relies on a vast array of components, from copper wire to specialized connectors. Manufacturers manage complex global supply chains by:
- Sourcing materials from suppliers worldwide.
- Maintaining inventory to meet production demands.
- Navigating geopolitical and economic factors.
- Implementing just-in-time delivery systems.
With production facilities often spread across continents, they must balance regional market needs with local regulations.
4. Innovation and R&D
To stay competitive, automotive wiring harness manufacturers invest heavily in research and development (R&D). This includes:
- Developing lighter, more compact designs for fuel efficiency.
- Integrating technologies like fiber optics for high-speed data transmission.
- Creating harnesses for electric vehicles’ increased power demands.
- Exploring sustainable materials and processes.
Collaborations with universities and tech companies often drive these innovations.
5. Aftermarket Support
Beyond OEMs, manufacturers produce harnesses for the aftermarket, including replacement parts for repairs, custom harnesses for modifications, and solutions for specialty vehicles. This requires extensive catalogs, customization options, and technical support for diverse customers.
In essence, automotive wiring harness manufacturers are the backbone of vehicle electrical systems, balancing precision engineering with large-scale production and constant innovation.
Challenges Facing the Industry
The automotive wiring harness manufacturing sector faces numerous challenges that test the resilience and adaptability of these companies. Here are the most pressing issues:
1. Technological Advancements
- Increasing Complexity: Features like advanced driver assistance systems (ADAS) and electrification demand harnesses with more wires and data capabilities.
- Miniaturization: Smaller vehicles require compact, lightweight harnesses without sacrificing performance.
- New Technologies: Electric vehicles and fiber optics necessitate new materials and expertise.
2. Cost Pressures
- Price Competition: Low-cost regions intensify competition, pushing manufacturers to reduce costs while maintaining quality.
- Raw Material Costs: Fluctuations in copper prices impact profitability.
- Labor Costs: Manual labor remains essential, and rising wages drive companies to automate or relocate.
3. Supply Chain Issues
- Geopolitical Risks: Trade tensions and tariffs disrupt material flows.
- Logistics: Global pandemics and semiconductor shortages highlight vulnerabilities.
- Component Shortages: Delays in one area can halt production.
4. Quality and Reliability Demands
- Zero-Defect Expectations: OEMs require defect rates in parts per million, necessitating rigorous testing.
- Durability: Harnesses must endure harsh conditions over a vehicle’s lifetime.
- Traceability: Detailed records are essential for recalls or quality issues.
5. Regulatory Compliance
- Safety Standards: Compliance with standards like ISO 26262 is critical.
- Environmental Regulations: Rules like the EU’s End-of-Life Vehicles Directive demand recyclability.
- Regional Variations: Global manufacturers must adapt to diverse frameworks.
6. Sustainability Pressures
- Eco-Friendly Materials: Demand grows for recyclable or biodegradable options.
- Energy Efficiency: Manufacturers face pressure to reduce emissions in production.
- Circular Economy: Designing for end-of-life recycling is increasingly important.
These challenges require automotive wiring harness manufacturers to be agile, innovative, and strategic to thrive in this demanding industry.
Case Studies: Leading Manufacturers and Innovations
To understand how automotive wiring harness manufacturers address these challenges, let’s examine some real-world examples:
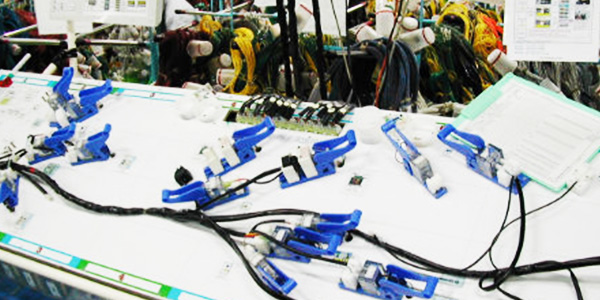
1. Yazaki Corporation: Lightweight Solutions
Yazaki, a global leader, introduced its “Ultra-Lightweight Wiring Harness” using aluminum wires and thinner insulation, reducing weight by up to 30%. This tackles fuel efficiency and cost concerns simultaneously.
2. Aptiv PLC: Automation and Digitalization
Aptiv’s “Smart Factory” leverages robotic assembly, AI-driven quality control, and digital twin technology to enhance efficiency and consistency, addressing labor costs and quality demands.
3. Lear Corporation: Electric Vehicle Focus
Lear has developed high-voltage harnesses for EVs, capable of handling 800 volts and integrating thermal management. This positions them as a key player in the electrification trend.
4. Sumitomo Electric Industries: Sustainability
Sumitomo uses halogen-free, recyclable materials and energy-efficient processes, reducing CO2 emissions by 20% per unit. This aligns with environmental regulations and customer preferences.
5. TE Connectivity: Collaborative Innovation
TE partners with research institutions to develop “smart” harnesses with sensors for self-diagnosis, enhancing reliability and addressing technological complexity.
6.Gvtong Electric
The best wiring harness for EVs in China, Lear has developed high-voltage harnesses for EVs, capable of handling 800 volts and integrating thermal management.
The best wiring harness for EVs in China, Lear has developed high-voltage harnesses for EVs, capable of handling 800 volts and integrating thermal management.
These examples showcase how automotive wiring harness manufacturers drive innovation to overcome industry challenges.
Future Trends in Automotive Wiring Harness Manufacturing
The industry is poised for transformation as new trends emerge. Here’s what lies ahead:
1. Electrification
EVs demand high-voltage harnesses (400-800V), advanced battery management wiring, and fast-charging solutions with cooling systems.
2. Autonomous Driving
Self-driving cars require high-bandwidth data networks, redundant wiring for safety, and electromagnetic compatibility, potentially incorporating fiber optics.
3. Lightweighting
Alternative materials like aluminum and compact designs will reduce weight and save space, improving efficiency.
4. Sustainability
Eco-friendly materials, recyclable designs, and energy-efficient production will meet growing environmental demands.
5. Advanced Manufacturing
3D printing, robotic assembly, and AI-driven quality control will enhance flexibility and precision.
6. Smart Features
Self-diagnosing harnesses and integrated power-data cables could improve vehicle performance and maintenance.
Automotive wiring harness manufacturers must adapt to these trends through R&D, workforce development, and strategic partnerships.
Conclusion
Automotive wiring harness manufacturers are vital to the automotive industry, crafting the electrical systems that power modern vehicles. From their intricate design processes to their innovative responses to challenges, these companies enable automotive progress. As electrification, autonomy, and sustainability reshape the landscape, their role will only grow in importance. By investing in technology, skills, and collaboration, they will continue to connect the future of mobility—one wire at a time.