Blogs & News
We are focus on automotive wiring harness & connectors technology.
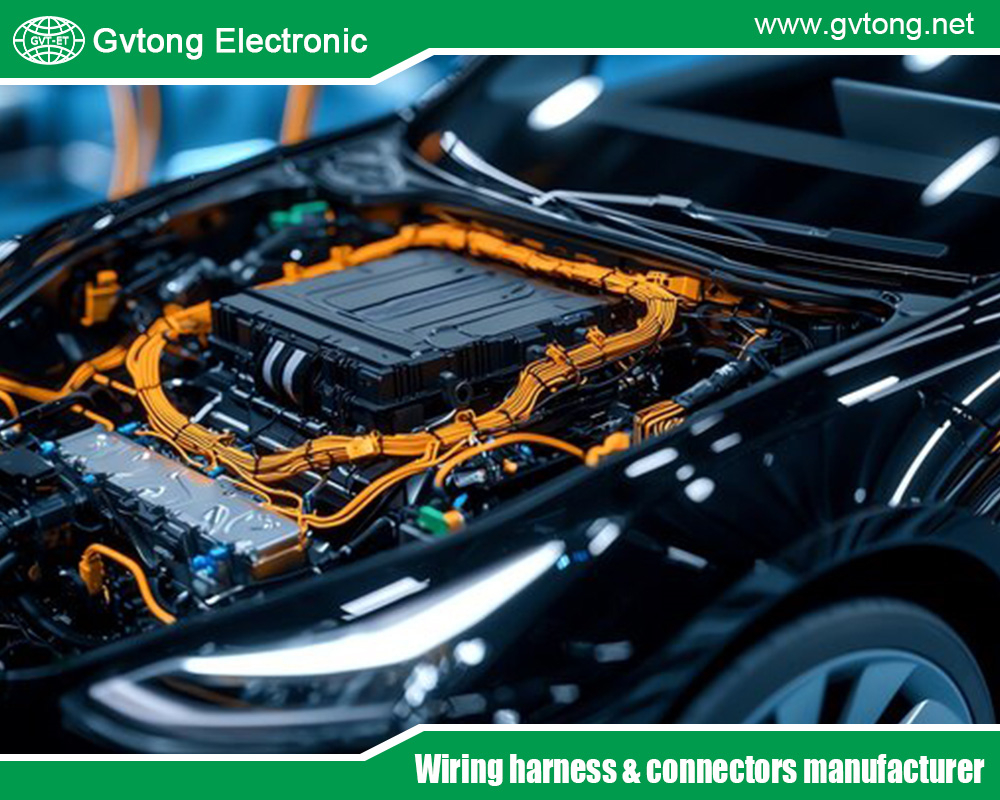
An MS Electrical Connectors Are Specifically Designed To Meet
- Gvtong Electronic
- Automated assembly connectors, automotive antenna connector, automotive coaxial connector, automotive data connector, automotive diagnostic connector, automotive high - frequency, automotive High voltage connector, automotive hybrid connector, automotive Low voltage connector, Automotive Low Voltage Signal And Power Connector Solutions, automotive Oil-resistant Connectors, automotive optical fiber connector, automotive power distribution, Automotive power distribution connector, automotive Signal Connector, automotive vibration - resistant, automotive waterproof connectors, Cost-effective automotive connectors, electric vehicle EV connector supplier, energy storage connector manufacturers, EV charging connectors manufacturers, Halogen-free automotive connectors, high current connectors manufacturer, High Frequency And High Speed Connectors Manufacturer, High Voltage EV Battery Connector For Electric Vehicles, MS Electrical Connectors, MS Electrical Connectors Manufacturer, MS Electrical Connectors Supplier, Multi-variation connectors, Photovoltaic Connectors For Solar Panels, photovoltaic connectors manufacturers, Photovoltaic Solar Battery Connectors For Energy Storage Systems
- No Comments
An MS Electrical Connectors Are Specifically Designed To Meet
MS electrical connectors, commonly referred to as MIL-C-5015 connectors, represent a pinnacle of engineering designed to address the exacting requirements of military and industrial applications. Originally developed in the 1930s for military use, these circular threading connectors have earned a reputation for their durability, ease of installation, and versatility. Over time, their utility has expanded beyond the battlefield, finding applications in industries ranging from aerospace to commercial transportation. This 2000-word article explores how MS electrical connectors are specifically engineered to meet diverse and demanding needs, delving into their design features, applications, standards, and evolution.
Introduction to MS Electrical Connectors
MS electrical connectors emerged from the necessity to provide reliable electrical connections in the harshest of environments—military operations. Known formally as MIL-C-5015 connectors, they adhere to strict military specifications that ensure performance under extreme conditions. Their circular design, coupled with a threaded coupling mechanism, allows for secure and rapid assembly without the need for specialized tools. This attribute, combined with their robustness and adaptability, has made MS connectors a staple not only in defense but also in industrial and commercial sectors. In this article, we will examine the specific attributes that enable MS connectors to fulfill such a broad spectrum of requirements.
Key Features of MS Connectors
Ease of Installation
One of the standout features of MS connectors is their tool-free assembly. The threaded design allows technicians to connect or disconnect them by simply rotating the barrel into the receptacle. This was a critical advantage for military personnel who often operated in confined spaces or under time pressure, such as inside aircraft or on active battlefields. The simplicity of installation reduces downtime and enhances operational efficiency, a benefit that translates seamlessly into industrial settings where quick maintenance is equally valuable.
Durability and Reliability
MS connectors are engineered to endure punishing conditions—extreme temperatures, vibration, moisture, and dust. Their high reliability stems from robust construction, often utilizing materials like aluminum alloys that resist corrosion and wear. With a high power capacity, these connectors can handle significant electrical loads without degradation, making them ideal for heavy-duty applications. Whether powering military communication systems or industrial machinery, MS connectors maintain consistent performance where failure is not an option.
Versatility
The versatility of MS connectors is evident in their range of configurations. Available in various shell sizes and pin counts—up to eighteen contacts—they cater to diverse electrical needs. Three contact types—solder, PC tail, and crimp—offer flexibility in assembly methods, with crimping being the most common due to its reliability. Additionally, MS connectors can be customized with waterproofing or constructed from alternative materials like plastics for specific uses, enhancing their adaptability across different environments.
Meeting Military Specifications
MS connectors are purpose-built to comply with stringent military standards, often referred to as MIL-Spec. These specifications, such as those outlined in the MIL-C-5015 standard, mandate exceptional durability, environmental resistance, and electrical performance. For instance, MS Single Wire Waterproof Connectors are designed to meet these exacting criteria, undergoing rigorous testing to ensure they withstand moisture ingress and mechanical stress. This makes them indispensable in military vehicles where exposure to water and rough terrain is routine.The connectors’ design also prioritizes secure connections. Crimping, the preferred method for attaching pins or sockets to wires, ensures a strong, vibration-resistant bond. Moreover, the convention of installing the pin (male) section on the ground side of a circuit enhances safety and operational integrity, a practice rooted in electrical engineering standards.
Types of MS Connectors
MS connectors come in multiple variants tailored to specific needs:
- Single Wire Waterproof Connectors: Highlighted by manufacturers like Amerline, these are optimized for applications requiring moisture resistance, such as military vehicle lighting systems. Their MIL-Spec compliance guarantees performance in wet conditions.
- Multi-Pin Variants: With shell sizes accommodating up to eighteen pins, these connectors support complex wiring needs in equipment like aircraft avionics or industrial control systems.
- Material Variants: Options range from durable aluminum alloys for rugged environments to lightweight plastics for applications where weight reduction is critical.
This diversity allows MS connectors to be fine-tuned for specific operational demands, whether it’s resisting corrosion in marine settings or supporting high-density connections in compact machinery.
Real-World Applications
Military Uses
In military contexts, MS connectors are ubiquitous—found in aircraft, naval vessels, ground vehicles, and communication gear. Their ability to function reliably amidst vibration, shock, and extreme weather makes them vital for mission-critical systems. For example, in a fighter jet, MS connectors link navigation and weapon systems, ensuring uninterrupted performance during high-stress maneuvers.
Industrial Applications
Beyond defense, MS connectors excel in industrial environments. In robotics, they connect motors and sensors, enduring constant movement and dust exposure. Manufacturing equipment relies on their high power capacity to drive heavy loads, while their ease of maintenance minimizes production interruptions.
Commercial Sectors
In the commercial realm, MS connectors are integral to vehicles like buses and trucks, particularly in lighting and control systems. Their durability ensures longevity in vehicles subjected to road vibrations and weather extremes, while their versatility supports varied electrical configurations.
Installation and Maintenance
Proper installation is key to maximizing MS connector performance. Crimping contacts requires precision tools to ensure a secure fit, while the threaded assembly must be correctly aligned to avoid cross-threading. Maintenance involves periodic checks—testing bonding connections for resistance and inspecting for wear or corrosion. Hardware selection for attachments should balance mechanical strength and ease of use, ensuring long-term reliability.
Standards and Specifications
MS connectors adhere to MIL-DTL standards, which dictate everything from material composition to electrical ratings. The MIL-C-5015 specification, for instance, outlines requirements for circular connectors with threaded couplings, ensuring uniformity and quality across manufacturers. While other standards like MIL-DTL-83513 cover different connector types, they reflect the broader military emphasis on precision and resilience that MS connectors embody.
Evolution of MS Connectors
Since their inception in the 1930s, MS connectors have evolved significantly. Early designs focused on basic reliability for military radios and vehicles, but advancements in materials—like corrosion-resistant alloys—and manufacturing techniques have broadened their scope. The introduction of waterproof variants in later decades addressed emerging needs in naval and outdoor applications, while crimp contacts improved installation efficiency. This ongoing refinement ensures MS connectors remain relevant as technology advances.
Comparison to Other Connectors
MS connectors stand out against alternatives due to their unique blend of features. Unlike many commercial connectors requiring tools for assembly, MS connectors’ hand-installable design saves time. Their environmental resilience surpasses that of standard industrial connectors, which may falter under extreme conditions. Compared to newer connector types with push-lock mechanisms, MS connectors’ threaded coupling offers superior security in high-vibration settings, making them a preferred choice in aerospace and defense.
The Future of MS Connectors
Looking ahead, MS connectors are poised to adapt to emerging trends. The rise of electric vehicles and renewable energy systems presents new opportunities—high-power variants could support EV charging infrastructure, while lightweight materials might enhance solar panel arrays. Advances in EMI/RFI shielding could further their use in sensitive electronics, ensuring they remain a cornerstone of connectivity solutions.
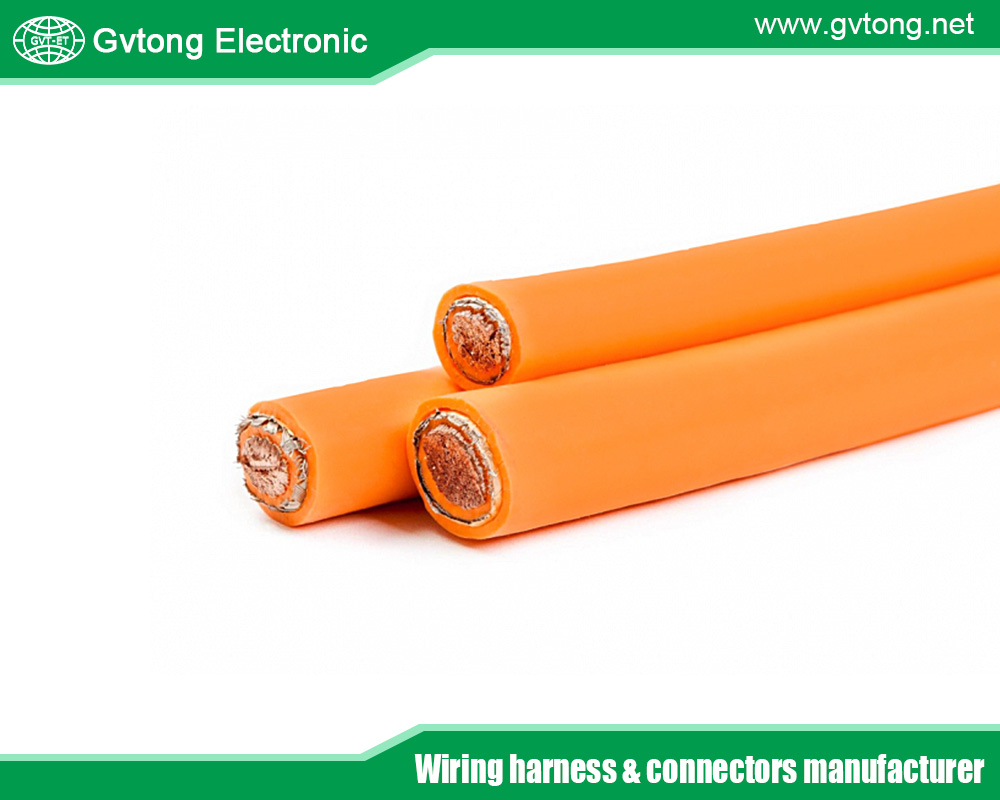
Conclusion
MS electrical connectors are meticulously designed to meet the rigorous demands of military specifications and beyond. Their ease of use, durability, and versatility have cemented their role across diverse industries, from powering fighter jets to enabling industrial automation. Through adherence to strict standards, continuous evolution, and practical design features, MS connectors exemplify engineering tailored to specific needs. As technology progresses, their adaptability ensures they will continue to meet the challenges of tomorrow, delivering reliable performance where it matters most.
For more about an MS electrical connectors are specifically designed to meet, you can pay a visit to Gvtong at https://www.gvtong.net/ for more info.
Recent Posts
The Role and Technical Advantages of 7-Cavity Connectors
Automotive Power Distribution
Tags
Recommended Products
-
GH Series-DCDC Through-the-Wall Terminal B
-
DCDC wall-through terminal – with protective cover
-
The battery PACK is packed with copper-aluminum busbar
-
Photovoltaic connector – Wire end socket
-
GE Series-WTB 6pin Connector Plug
-
Signal connector-8 core-12#
-
Five-in-one terminal
-
Photovoltaic Connector-Board Socket