Comprehensive Guide to Automotive Connectors Manufacturers
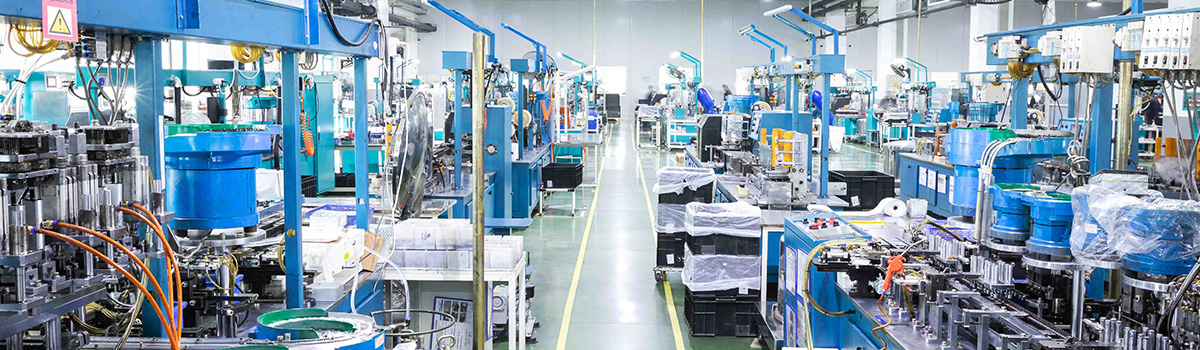
Table of Contents
ToggleIntroduction to Automotive Connectors
Types of Automotive Connectors
Manufacturing Process of Automotive Connectors
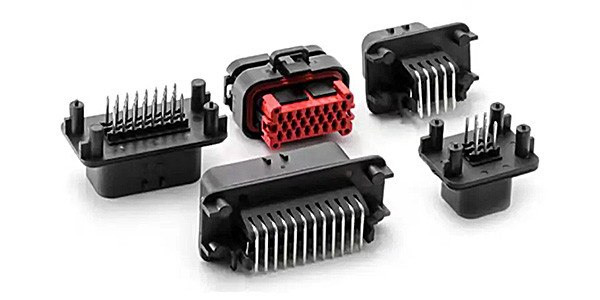
- Plastics: The connector housing is typically made from heat-resistant, durable plastics like polyamide or polyester.
- Metals: Pins and contacts use conductive metals such as copper, brass, or phosphor bronze, often plated with gold, silver, or tin to enhance conductivity and resist corrosion.
- Seals and Gaskets: Rubber or silicone seals protect against dust and moisture, critical for connectors in exposed areas.
- Injection Molding: Molten plastic is injected into molds to form the housing, cooled, and ejected with precision.
- Stamping and Forming: Metal sheets are stamped and shaped into pins or sockets, ensuring consistent dimensions.
- Plating: Contacts are coated with thin layers of metal to improve performance and longevity.
- Assembly: Automated machinery assembles the components, inserting pins into housings and adding seals, ensuring uniformity.
- Electrical Testing: Checks for continuity, insulation resistance, and voltage drop.
- Mechanical Testing: Assesses durability against vibrations, shocks, and repeated mating cycles.
- Environmental Testing: Simulates exposure to heat, cold, humidity, and chemicals.
Technology and Innovation in Automotive Connectors
Market Overview of Automotive Connectors
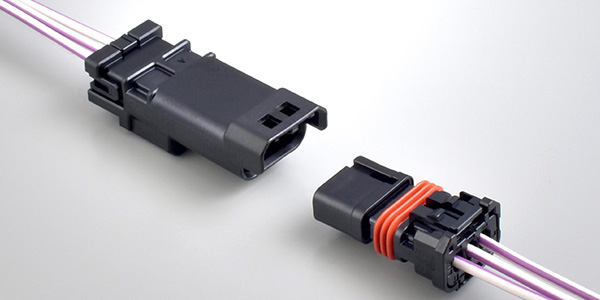
- TE Connectivity: Offers a broad range of connectors, excelling in EV and high-speed data solutions.
- Aptiv PLC: Focuses on mobility innovations, including connectors for autonomous vehicles.
- Yazaki Corporation: A leader in wiring harnesses and connectors, with a strong Asian presence.
- Sumitomo Electric Industries: Known for durable connectors across diverse applications.
- Trends: The shift to EVs and safety-critical systems (e.g., ADAS) boosts demand for specialized connectors. Sustainability is also a growing focus.
- Challenges: Standardization varies across automakers, complicating production. Supply chain disruptions and raw material costs further test manufacturers.
Leading Automotive Connectors Manufacturers
1. TE Connectivity
Overview: A global connectivity leader with a strong automotive focus.
Products: High-voltage connectors for EVs, high-speed data connectors, and sensor solutions.
Innovations: Pioneering EV charging connectors and compact designs for modern vehicles.
Market Position: A dominant player known for reliability and cutting-edge technology.
2. Aptiv PLC
Overview: Formerly part of Delphi, Aptiv targets future mobility solutions.
Products: Connectors for data, power, and signal applications.
Innovations: High-bandwidth connectors for autonomous driving and sustainable designs.
Market Position: A forward-thinker with a growing presence in advanced tech.
3. Yazaki Corporation
Overview: A Japanese giant in automotive wiring and connectors.
Products: Wire-to-wire, multi-pin, and ECU connectors.
Innovations: Lightweight, compact connectors for efficiency.
Market Position: Strong in Asia, with deep ties to major automakers.
4. Sumitomo Electric Industries
Overview: A diversified firm with a robust automotive division.
Products: Connectors for engines, lighting, and infotainment.
Innovations: High-durability connectors for extreme conditions.
Market Position: Valued for quality and versatility
5. Gvtong Electric
Overview: A Chinese giant in automotive wiring and connectors.
Products: Wiring harness & connectors for EVs.
Innovations: High-durability connectors for extreme conditions.
Market Position: Valued for quality and versatility.
Future Outlook for Automotive Connectors Manufacturers
- 5G Connectivity: Faster networks will demand connectors for high-frequency data transfer.
- Wireless Charging: EVs may shift toward contactless systems, influencing connector design.
- Advanced Materials: Graphene or conductive polymers could create lighter, more efficient connectors.
- Consolidation: Mergers and acquisitions may reshape the competitive landscape.
- Localization: Regional production could rise to counter supply chain risks.
- Customization: Tailored solutions for automakers can set manufacturers apart.
- Sustainability: Green practices and products appeal to regulators and consumers.
- Aftermarket: Services like repairs or upgrades offer new revenue streams.