Blogs & News
We are focus on automotive wiring harness & connectors technology.
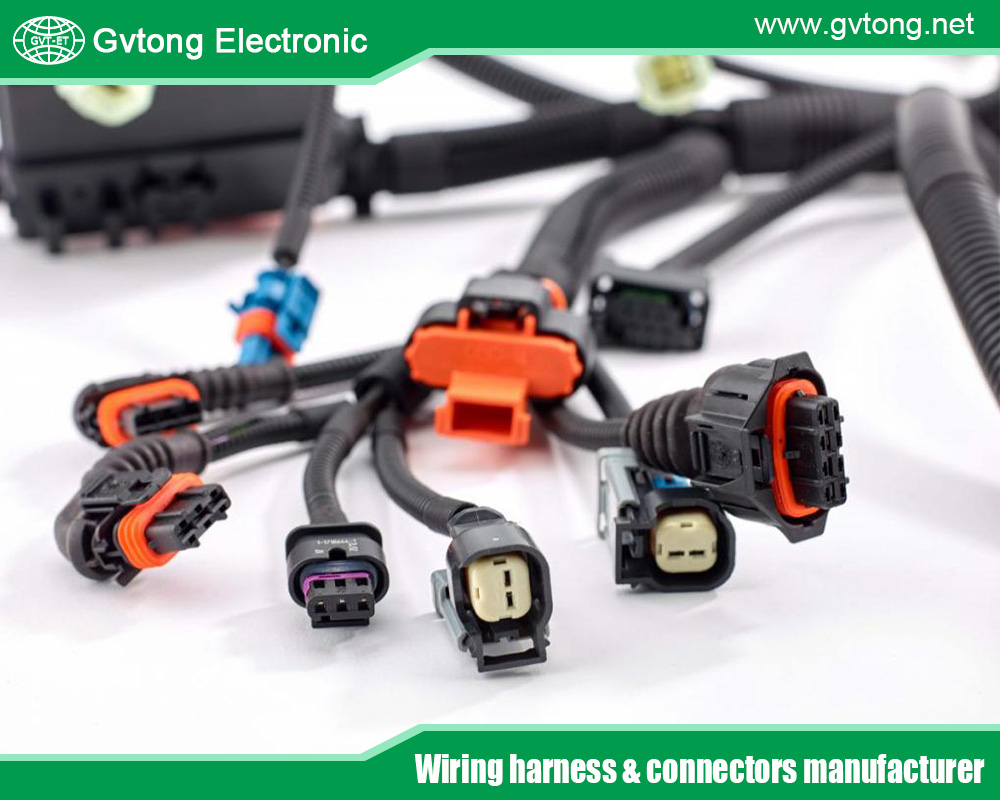
Development History and Breakthroughs of Automotive Cavity Connectors
- Gvtong Electronic
- 48V board net connectors, automotive antenna connector, automotive cavity connectors, automotive cavity connectors manufacturer, automotive cavity connectors supplier, automotive coaxial connector, automotive data connector, automotive diagnostic connector, automotive electrical connector, automotive high - frequency, Automotive high - frequency connector, automotive High voltage connector, automotive hybrid connector, automotive Low voltage connector, automotive Oil-resistant Connectors, automotive optical fiber connector, automotive power distribution, Automotive power distribution connector, automotive Signal Connector, Automotive temperature - resistant connector, automotive vibration - resistant, Automotive vibration - resistant connector, automotive waterproof connectors, Automotive-grade AEC-Q200 connectors, cavity connectors, Redundant safety connectors, Thermal management connectors, Wireless charging connectors
- No Comments
Development History and Breakthroughs of Automotive Cavity Connectors
Cavity connectors, the unsung heroes of automotive electrical systems, have played a pivotal role in the evolution of vehicles from rudimentary mechanical machines to sophisticated, electrified, and autonomous platforms. These connectors, which house electrical terminals to facilitate power, signal, and data transmission, are integral to wiring harnesses that form the nervous system of modern vehicles. From single-cavity designs in early automobiles to advanced multi-cavity connectors in electric and autonomous vehicles, their development mirrors the industry’s technological progress. This article provides an in-depth exploration of the history, breakthroughs, and future potential of automotive cavity connectors. By examining their design evolution, material advancements, and adaptation to emerging trends like electrification and connectivity, we aim to underscore their critical role in shaping automotive innovation. As vehicles become more complex, cavity connectors continue to enable reliable, efficient, and compact electrical interfaces, driving the industry toward a future of smarter, greener, and safer mobility.
Early Beginnings of Automotive Electrical Systems
The history of automotive cavity connectors begins with the dawn of the automobile in the late 19th century. Early vehicles, like the 1886 Benz Patent-Motorwagen, relied on rudimentary ignition systems with minimal electrical components. Wiring was basic, often using single-point connections for spark plugs or lighting, with no standardized connectors. By the 1920s, as vehicles incorporated starters, generators, and basic lighting, the need for reliable electrical interfaces emerged. Early connectors were simple, single-cavity designs, typically hand-soldered and made from brass or copper, offering basic insulation with rubber or cloth.
The 1940s and 1950s marked a turning point as vehicles became more complex. The introduction of 12-volt electrical systems and the proliferation of accessories like radios and heaters necessitated multi-cavity connectors to manage multiple circuits. These early multi-cavity designs, often two- or three-cavity, were bulky and prone to corrosion, lacking the sealing and durability required for harsh automotive environments. However, they laid the groundwork for standardized wiring harnesses, which became essential as production scaled during the post-World War II automotive boom.
By the 1960s, the rise of electronic ignition and fuel injection systems increased the demand for connectors capable of handling higher currents and signals. Manufacturers like AMP (now TE Connectivity) and Deutsch introduced molded plastic housings, improving insulation and reducing weight. These early cavity connectors, though limited in mating cycles and environmental resistance, set the stage for the sophisticated designs that would follow.
Rise of Standardized and Sealed Connectors
The 1970s and 1980s saw significant advancements in cavity connector design, driven by stricter safety regulations and the growing complexity of automotive electronics. The introduction of engine control units (ECUs) and sensors for emissions control required connectors that could handle precise signal transmission. Multi-cavity connectors, ranging from 2 to 12 cavities, became standard in wiring harnesses. These connectors used thermoplastic housings, such as nylon or polybutylene terephthalate (PBT), offering better heat and chemical resistance than earlier materials.
A major breakthrough during this period was the development of sealed connectors. Automotive environments, particularly under-hood applications, exposed connectors to moisture, dust, and extreme temperatures. Silicone seals and gaskets enabled connectors to achieve IP65 or higher ingress protection ratings, ensuring reliability in harsh conditions. Companies like Molex and Aptiv introduced sealed multi-cavity connectors, which became critical for applications like fuel injectors and oxygen sensors.
Standardization also played a key role. Industry standards like USCAR and ISO 16750 defined performance criteria for connectors, ensuring compatibility across manufacturers and regions. Locking mechanisms, such as positive latches and secondary locks, improved connection reliability under vibration, a common issue in vehicles. By the late 1980s, cavity connectors with terminal position assurance (TPA) features emerged, preventing misalignment and ensuring secure electrical contacts.
The shift to modular wiring harnesses further accelerated connector adoption. Multi-cavity connectors allowed manufacturers to pre-assemble harnesses, streamlining vehicle assembly and reducing costs. These advancements made cavity connectors indispensable, supporting the growing number of electrical systems in vehicles, from power windows to early anti-lock braking systems (ABS).
Technological Breakthroughs in the 1990s and 2000s
The 1990s and 2000s marked a golden era for cavity connector innovation, driven by the rise of electronics-heavy vehicles. The introduction of Controller Area Network (CAN) bus systems revolutionized automotive communication, enabling real-time data exchange between ECUs, sensors, and actuators. Multi-cavity connectors, particularly 3- to 6-cavity designs, became critical for CAN bus interfaces, supporting low-latency, error-free data transmission. These connectors used gold- or tin-plated terminals to minimize contact resistance and ensure signal integrity.
Material advancements were a significant breakthrough. High-performance thermoplastics, such as polyphenylene sulfide (PPS), offered superior thermal stability, withstanding temperatures up to 150°C. This was crucial as under-hood environments grew hotter with turbocharged engines and compact designs. Additionally, corrosion-resistant coatings and advanced sealing technologies, like multi-lip silicone gaskets, extended connector lifespans in extreme conditions.
Miniaturization became a focus as vehicle designs prioritized space efficiency. Compact multi-cavity connectors, some as small as 15 mm in length, allowed integration into tight spaces without sacrificing performance. For example, TE Connectivity’s Mini-Fit connectors, introduced in the 2000s, offered high-density terminal arrangements, supporting applications like infotainment and climate control systems.
Another breakthrough was the development of high-mating-cycle connectors. As vehicles incorporated more serviceable components, connectors needed to withstand repeated connections and disconnections (often exceeding 100 cycles). Innovations like spring-loaded terminals and robust locking systems addressed this need, improving durability and ease of maintenance.
The rise of hybrid electric vehicles (HEVs) in the early 2000s introduced new challenges. Cavity connectors had to support both low-voltage control circuits and high-voltage power systems. Specialized high-voltage connectors, often with 2- to 4-cavity designs, emerged to handle currents up to 50A, incorporating safety features like interlocks to prevent arcing. These advancements laid the foundation for the electrification revolution that followed.
Modern Applications and the Electrification Era
The 2010s and 2020s ushered in a new era for cavity connectors, driven by the rapid adoption of electric vehicles (EVs), autonomous driving, and connectivity. EVs, with their high-voltage batteries (400V to 800V), required connectors capable of handling significant power loads while ensuring safety. Multi-cavity connectors, particularly 3- to 8-cavity designs, are used in battery management systems (BMS) to connect sensors monitoring voltage, temperature, and state of charge. For example, a 3-cavity connector might link a thermistor to the BMS, ensuring safe battery operation.
Autonomous vehicles, with their reliance on LIDAR, radar, and cameras, demand connectors that support high-speed data transmission. Multi-cavity connectors facilitate Automotive Ethernet and CAN-FD (Flexible Data-Rate) protocols, enabling real-time communication for advanced driver-assistance systems (ADAS). Their compact designs and shielding for electromagnetic compatibility (EMC) ensure reliable performance in data-intensive applications.
Connectivity trends, including vehicle-to-everything (V2X) communication and over-the-air (OTA) updates, have increased the need for robust data pathways. Cavity connectors, often integrated into communication modules, support low-latency data transfer for features like 5G connectivity and traffic signal prioritization. Their standardized designs ensure compatibility across vehicle platforms, from luxury EVs to mass-market models.
In infotainment systems, multi-cavity connectors enable interfaces for USB ports, speakers, and touchscreens, enhancing user experience. Their versatility also extends to lighting systems, where they connect LED modules, contributing to energy efficiency and design flexibility. According to market reports, the automotive connector market, valued at $15 billion in 2023, is projected to grow at a 6% CAGR through 2030, with cavity connectors playing a central role.
Breakthroughs in Materials and Manufacturing
Recent breakthroughs in materials and manufacturing have elevated cavity connectors to new levels of performance. Advanced thermoplastics, like liquid crystal polymers (LCPs), offer exceptional heat resistance (up to 200°C) and dimensional stability, ideal for high-voltage EV applications. Conductive coatings, such as silver or nickel, reduce contact resistance, improving efficiency in power-intensive systems.
Sealing technologies have also advanced. Multi-cavity connectors now achieve IP69K ratings, resisting high-pressure water jets and extreme environmental conditions. This is critical for EVs and autonomous vehicles operating in diverse climates. Additionally, eco-friendly materials, like recyclable plastics and lead-free terminals, align with sustainability goals, reducing the environmental impact of connector production.
Smart manufacturing has transformed connector production. Automated assembly lines, coupled with AI-driven quality control, ensure precision and consistency. For instance, laser welding and ultrasonic bonding improve terminal-to-housing integrity, reducing failure rates. Companies like Aptiv have introduced connectors with integrated diagnostics, allowing real-time monitoring of connection health, a game-changer for autonomous vehicle reliability.
Additive manufacturing (3D printing) is another breakthrough, enabling rapid prototyping of custom connector designs. This allows manufacturers to tailor connectors for specific vehicle applications, reducing development time and costs. These innovations have made cavity connectors more reliable, compact, and cost-effective, supporting the automotive industry’s rapid evolution.
Challenges and Future Directions
Despite their advancements, cavity connectors face challenges in meeting the demands of next-generation vehicles. The shift to 800V EV architectures requires connectors with enhanced insulation and thermal management to prevent overheating and arcing. While high-voltage connectors are emerging, adapting multi-cavity designs for these applications remains a focus of innovation.
Miniaturization continues to be a challenge as vehicles incorporate more electronics in limited spaces. Ultra-compact connectors, with cavity counts as high as 20 in a small footprint, are being developed using micro-molding and high-density terminal layouts. Maintaining signal integrity in these designs, especially for high-speed data, requires advanced shielding and noise suppression.
The rise of solid-state batteries, expected to enter mass production by 2030, will demand connectors with superior thermal and electrical performance. Multi-cavity connectors could evolve to support auxiliary circuits in these systems, such as cooling or monitoring. Similarly, vehicle-to-grid (V2G) systems will require connectors with high mating cycles to support frequent charging.
Future innovations may include smart connectors with embedded sensors to monitor temperature, current, or wear, enhancing predictive maintenance. Wireless power transfer, though still nascent, could reduce reliance on physical connectors, but cavity connectors will remain critical for control and data circuits. Collaboration between automakers and connector manufacturers will drive these advancements, ensuring compatibility with emerging standards like Automotive Ethernet and ISO 21434 (cybersecurity).
Conclusion
The development of automotive cavity connectors reflects the industry’s journey from simple mechanical vehicles to complex, electrified, and autonomous systems. From the basic single-cavity designs of the early 20th century to today’s sophisticated multi-cavity connectors, breakthroughs in materials, sealing, miniaturization, and manufacturing have made them indispensable. These connectors enable critical functions, from battery management in EVs to data transmission in autonomous vehicles, aligning with trends like electrification, connectivity, and sustainability. As the automotive industry evolves, cavity connectors will continue to adapt, addressing challenges like high-voltage demands and space constraints through innovations in smart materials and production techniques. Their role in ensuring reliable, efficient, and compact electrical interfaces underscores their importance in shaping the future of mobility. By bridging the gap between legacy systems and cutting-edge technologies, cavity connectors are not just supporting automotive progress—they are driving it forward.
For more about the development history and breakthroughs of automotive cavity connectors, you can pay a visit to Gvtong at https://www.gvtong.net/ for more info.