EV Wire Connectors
The Unsung Heroes of Electric Vehicles
EV Wire Connectors: The Unsung Heroes of Electric Vehicles
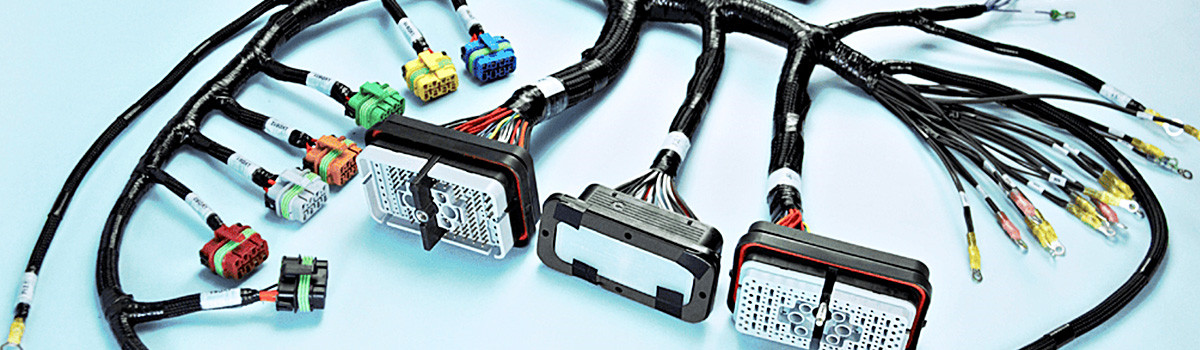
Table of Contents
ToggleIntroduction to EV Wire Connectors
Electric vehicles (EVs) are transforming the automotive landscape, shifting the industry from fossil fuel reliance to sustainable, electrically powered transportation. At the core of this revolution lies a sophisticated network of electrical systems, where EV wire connectors serve as critical components. These connectors are the linchpins that ensure seamless transmission of electrical power and signals, enabling EVs to operate efficiently, safely, and reliably.
EV wire connectors are specialized devices designed to join electrical circuits, providing both electrical conductivity and mechanical stability. In an electric vehicle, they connect everything from the high-voltage battery to the motor, to the low-voltage systems powering sensors and infotainment. Unlike connectors in traditional internal combustion engine (ICE) vehicles, which primarily handle low-voltage systems, EV wire connectors must accommodate a broader range of electrical demands, including high voltages up to 800V or more and currents reaching hundreds of amps.
Their significance cannot be overstated. A single faulty connector can disrupt power flow, compromise vehicle performance, or pose safety hazards like electrical fires or shocks. As EVs become more prevalent—projected to account for over 30% of global vehicle sales by 2030 according to industry forecasts—the role of EV wire connectors in ensuring vehicle reliability and consumer safety grows increasingly vital.
This article dives deep into the world of EV wire connectors, exploring their types, design intricacies, material composition, manufacturing processes, testing protocols, and emerging innovations. By the end, readers will gain a comprehensive understanding of how these components drive the EV revolution forward, bridging the gap between cutting-edge technology and practical application.
Types of EV Wire Connectors
EV wire connectors are not a one-size-fits-all solution. They vary widely based on their application within the vehicle, falling into three primary categories: high-voltage connectors, low-voltage connectors, and charging connectors. Each type is engineered to meet specific electrical, mechanical, and environmental demands, reflecting the diverse needs of an EV’s architecture.

High-Voltage Connectors
High-voltage connectors are the heavy lifters of the EV world, tasked with managing the substantial electrical loads that power the vehicle’s core systems. These connectors link the battery pack to the inverter, the inverter to the electric motor, and other high-power components. In modern EVs, operating voltages typically range from 400V to 800V, with currents often exceeding 200 amps, especially in high-performance models.
Key Characteristics
- High Current-Carrying Capacity: These connectors must handle large currents without overheating. For instance, a connector in a 400V system delivering 100 kW of power must sustain 250 amps, requiring robust conductive pathways.
- Low Contact Resistance: Minimizing resistance at the connection point reduces power loss and heat buildup, critical for efficiency and safety.
- High Insulation Resistance: With voltages in the hundreds, insulation must prevent leakage or arcing, often exceeding 1000 MΩ in specification.
- Mechanical Durability: EVs experience constant vibration and thermal cycling, so connectors feature rugged designs with locking mechanisms to maintain integrity.
- Safety Features: Interlocks—mechanical or electrical switches that disable power during disconnection—prevent accidental shocks or arcs.
Applications and Examples
High-voltage connectors are found in the powertrain and energy storage systems. A notable example is TE Connectivity’s HVA 280 series, designed for currents up to 280 amps and voltages up to 600V, commonly used in hybrid and electric vehicles. Another is Amphenol’s RADSOK technology, which enhances current capacity through a unique contact design, ideal for high-power EV applications.
Design Challenges
Designing high-voltage connectors involves balancing size, weight, and performance. They must be compact to fit within tight vehicle spaces yet robust enough to handle extreme conditions. Shielding against electromagnetic interference (EMI) is also crucial, as high currents can disrupt nearby electronics.
Low-Voltage Connectors
While high-voltage connectors power the drivetrain, low-voltage connectors manage the vehicle’s nervous system—the myriad electronic components that control everything from headlights to climate systems. These connectors typically operate at 12V or 48V, reflecting the legacy automotive electrical standard and newer mild-hybrid systems.
Key Characteristics
- Compactness: With dozens of electronic modules in modern EVs, space is limited, necessitating small, efficient designs.
- High Pin Density: Many low-voltage connectors support multiple signals—up to 50 or more pins in a single unit—enabling complex wiring harnesses.
- Environmental Resilience: Exposure to heat, humidity, and dust requires sealing and corrosion-resistant materials.
- Signal Integrity: For data-heavy applications like sensors or infotainment, EMI shielding ensures clean signal transmission.
Applications and Examples
Low-voltage connectors are ubiquitous, connecting sensors (e.g., temperature, proximity), control units (e.g., battery management systems), and user interfaces. The Molex Mini-Fit Jr. connector, with its compact footprint and reliable performance, is a popular choice, as is TE Connectivity’s MQS series, known for high-density signal applications in automotive environments.
Design Challenges
The challenge lies in miniaturization without sacrificing reliability. As EVs incorporate more electronics—think advanced driver-assistance systems (ADAS)—low-voltage connectors must evolve to support higher data rates and tighter tolerances.
Charging Connectors
Charging connectors bridge the gap between the EV and the external power grid, making them essential for recharging the battery. These connectors adhere to global standards, each tailored to specific regions, power levels, and charging speeds.
Key Standards and Characteristics
- Type 1 (SAE J1772): Predominant in North America, this single-phase AC connector supports up to 19.2 kW (240V, 80A). It’s simple, with five pins including power, ground, and communication lines.
- Type 2 (IEC 62196): Europe’s standard, offering single- or three-phase AC charging up to 43 kW. Its seven-pin design adds flexibility for higher power delivery.
- CCS (Combined Charging System): Built on Type 1 or Type 2, CCS adds two DC pins for fast charging, reaching 350 kW or more. It uses Power Line Communication (PLC) for smart charging coordination.
- CHAdeMO: Originating in Japan, this DC fast-charging standard delivers up to 400 kW, using the CAN bus protocol for vehicle-charger communication.
- Tesla Supercharger: Tesla’s proprietary DC connector offers high-speed charging (up to 250 kW) exclusively for its vehicles, with a sleek, user-friendly design.
Applications and Examples
Charging connectors are the user-facing side of EVs, found at home chargers, public stations, and Tesla’s Supercharger network. The CCS Combo 2, for instance, is widely adopted in Europe and North America for its versatility, while CHAdeMO remains strong in Japan and parts of Asia.
Design Challenges
Interoperability is a key concern—connectors must align with diverse charging infrastructures. Weatherproofing, durability (e.g., 10,000 mating cycles), and safety features like temperature sensors to prevent overheating are also critical.
Summary of Types
Together, high-voltage, low-voltage, and charging connectors form the backbone of an EV’s electrical system, each tailored to its role. Their diversity underscores the complexity of EV design, where EV wire connectors must adapt to both internal and external demands.
Design Considerations for EV Wire Connectors
Designing EV wire connectors is a multidisciplinary endeavor, blending electrical engineering, mechanical design, and materials science. Engineers must address a host of factors to ensure connectors perform reliably across an EV’s lifespan.
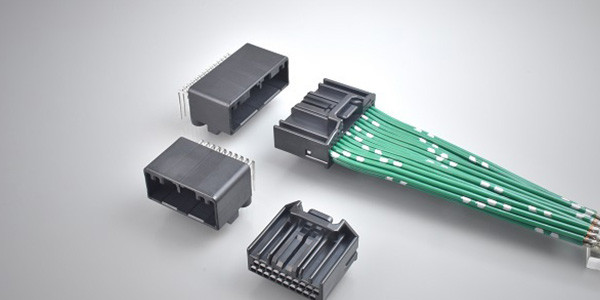
Electrical Requirements
- Voltage and Current: Connectors must support peak loads—e.g., 800V and 400A for high-voltage systems—without breakdown.
- Power Dissipation: Heat from resistance must be dissipated to avoid thermal damage, often requiring cooling or larger contact surfaces.
- Insulation: High dielectric strength materials prevent arcing, especially in high-voltage applications.
Mechanical Requirements
- Size and Weight: Compact, lightweight designs reduce vehicle mass and improve efficiency.
- Mating Cycles: Connectors must endure thousands of connections (e.g., 10,000 for charging connectors) without wear.
- Vibration Resistance: Automotive-grade connectors withstand 10-50G of vibration, per SAE standards.
Environmental Requirements
- Temperature Range: Operation from -40°C to 125°C is typical, covering extreme climates and heat from current flow.
- Moisture and Chemical Resistance: IP67 or higher ratings ensure protection against water, dust, and fluids like brake cleaner.
Safety Requirements
- Touch Protection: Finger-safe designs (e.g., IP2X) prevent accidental contact with live parts.
- Interlocks: High Voltage Interlock Loops (HVIL) disable power during maintenance, a must for high-voltage systems.
Electromagnetic Compatibility (EMC)
- Shielding: Metal or conductive polymer shields reduce EMI, critical near sensitive electronics.
- Filtering: Integrated capacitors or inductors suppress noise in signal lines.
Cost and Manufacturability
- Material Selection: Balancing performance with cost—e.g., tin plating vs. gold—impacts production economics.
- Scalability: Designs must suit high-volume automated assembly to meet EV market growth.
Case Study: High-Voltage Connector Design
Consider a 600V connector for an EV battery pack. Engineers might select a copper alloy contact with silver plating (for low resistance), a PPS housing (for heat resistance), and a silicone seal (for IP68 protection). The design would incorporate an HVIL and EMI shielding, tested to ISO 16750 standards, ensuring it meets both performance and regulatory needs.
Materials Used in EV Wire Connectors
The performance of EV wire connectors hinges on the materials used, each chosen for specific electrical, mechanical, and environmental properties.
Conductive Materials
- Copper Alloys: Brass or phosphor bronze contacts offer high conductivity (58 MS/m) and strength. Platings like silver (for high current) or tin (for cost) enhance durability.
- Aluminum: Used in busbars for weight savings, though less conductive than copper (37 MS/m).
Insulating Materials
- PBT (Polybutylene Terephthalate): Strong and stable up to 150°C, ideal for housings.
- PA66 (Polyamide 66): Tough and abrasion-resistant, common in low-voltage connectors.
- PPS (Polyphenylene Sulfide): Excels at 200°C+ and resists chemicals, suited for high-voltage applications.
Sealing Materials
- Silicone Rubber: Flexible and waterproof, used for gaskets with -50°C to 200°C range.
- EPDM: Cost-effective alternative with good weather resistance.
Other Materials
- Stainless Steel: Springs and clips resist corrosion in harsh conditions.
- Conductive Plastics: EMI shielding in lightweight designs.
Material Advancements
Recent innovations include graphene-enhanced coatings for contacts (improving conductivity) and bio-based plastics for sustainability, aligning with EV eco-goals.
Manufacturing Processes for EV Wire Connectors
Producing EV wire connectors involves precision techniques to ensure consistency and quality at scale.
Stamping and Forming
- Metal contacts are stamped from copper alloy sheets using progressive dies, then formed into pins or sockets via bending or coining.
Injection Molding
- Plastic housings are molded with high-pressure injection of molten PBT or PPS, cooled in seconds for high throughput.
Plating
- Electroplating applies silver or tin layers (1-5 µm thick) to contacts, enhancing conductivity and wear resistance.
Assembly
- Automated lines insert contacts into housings, attach seals, and crimp wires, with vision systems ensuring accuracy.
Quality Control
- In-line checks measure dimensions, plating thickness, and electrical continuity, rejecting defects instantly.
Automation Impact
Advanced robotics have cut production times by 30%, enabling millions of connectors annually to support EV demand.
Testing and Quality Assurance for EV Wire Connectors
Rigorous testing ensures EV wire connectors meet automotive standards like ISO 16750, SAE J1742, and UL 2251.
Electrical Tests
- Contact Resistance: <10 mΩ ensures efficiency.
- Insulation Resistance: >1000 MΩ prevents leakage.
- Dielectric Strength: 2-3 kV withstand without breakdown.
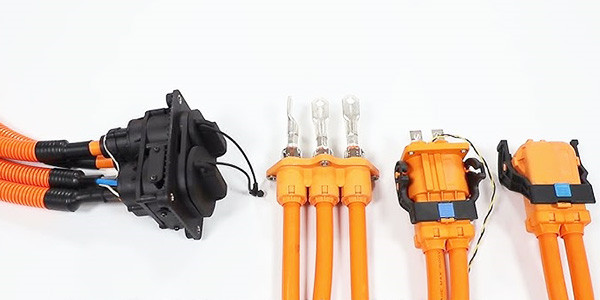
Mechanical Tests
- Mating Durability: 10,000 cycles for charging connectors.
- Vibration: 20G at 10-2000 Hz simulates road conditions.
Environmental Tests
- Thermal Cycling: -40°C to 125°C, 1000 cycles.
- Salt Spray: 96 hours per ASTM B117 for corrosion resistance.
Safety Tests
- HVIL Functionality: Confirms power cutoff during disconnection.
- Overload: Simulates short circuits to verify robustness.
Certification
Passing these tests earns compliance with IEC 62196 (charging connectors) or SAE J2929 (high-voltage systems), ensuring market readiness.
Future Trends and Innovations in EV Wire Connectors
The evolution of EVs is driving innovation in EV wire connectors, aligning with industry trends.
Higher Voltage Systems
- 800V+ architectures for faster charging demand connectors with enhanced insulation and current capacity.
Smart Connectors
- Embedded sensors monitor temperature and wear, feeding data to vehicle diagnostics.
Sustainable Materials
- Recyclable polymers and low-impact metals reduce environmental footprints.
Additive Manufacturing
- 3D printing accelerates prototyping, enabling complex, lightweight designs.
Wireless Influence
- While not replacing wire connectors, wireless tech may reduce low-voltage connector counts.
Example: Smart Charging Connectors
Future CCS connectors might integrate temperature sensors and AI to optimize charging rates, enhancing efficiency and safety.
Conclusion
EV wire connectors are the unsung heroes of electric vehicles, enabling the flow of power and data that defines modern mobility. From high-voltage powertrains to low-voltage electronics and charging interfaces, their diversity and precision reflect the complexity of EV engineering. Designed with meticulous attention to electrical performance, mechanical strength, and environmental resilience, these connectors underpin the safety and efficiency of every electric mile traveled.
As EVs advance—pushing towards higher voltages, smarter systems, and greener materials—EV wire connectors will continue to evolve, embodying the innovation that fuels this automotive revolution. Their story is one of engineering excellence, quietly connecting the future of transportation.