EV Wiring Harness: The Lifeline of Electric Vehicles
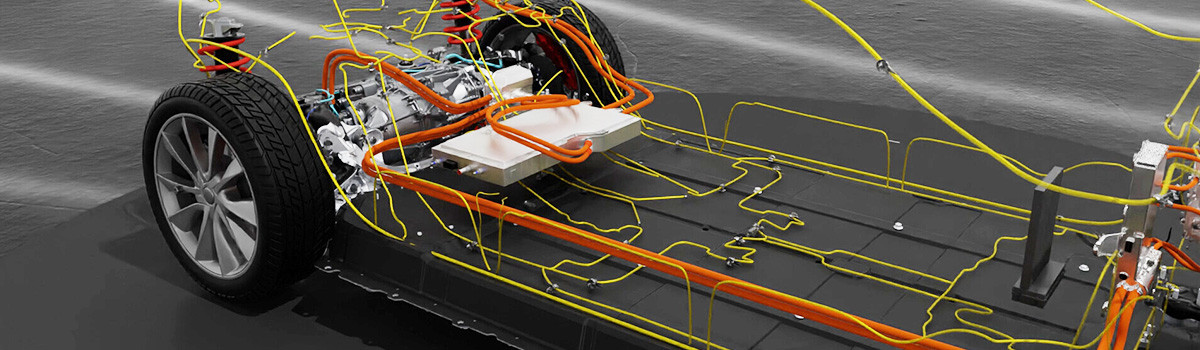
Table of Contents
ToggleIntroduction to EV Wiring Harnesses
Components of an EV Wiring Harness
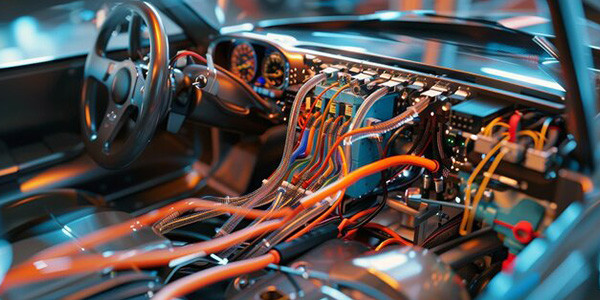
- High-Voltage Cables: These cables transmit power from the traction battery to the electric motor, onboard charger, and other high-power systems. Rated for voltages between 400V and 1,000V, they are typically constructed with thick conductors and heavy insulation to handle currents exceeding 200 amps. Shielding is often applied to mitigate electromagnetic interference (EMI), a critical consideration given the proximity of sensitive electronics in EVs.
- Low-Voltage Wires: Operating at 12V or 48V, these wires support control signals, sensors, and auxiliary systems such as lighting, infotainment, and climate control. They are smaller in gauge and often bundled alongside high-voltage cables within the harness.
- High-Voltage Connectors: These are engineered for safety and durability, featuring robust locking mechanisms, weatherproof seals, and insulation to prevent arcing or accidental disconnection. Standards such as SAE J1772 dictate their design for charging applications.
- Low-Voltage Connectors: Smaller and more numerous, these connectors link control units and sensors. They are designed for ease of assembly and maintenance, often using standardized pin configurations.
- Conduits and Grommets: These shield wires from abrasion, vibration, and environmental hazards like moisture and heat. Flexible conduits are commonly used in areas subject to movement.
- Shielding and Braiding: High-voltage cables are encased in metallic braids or foil to reduce EMI and protect signal integrity.
- Tapes and Sleeves: These provide additional insulation and bundling, keeping the harness organized and resistant to wear.
Design Considerations for EV Wiring Harnesses
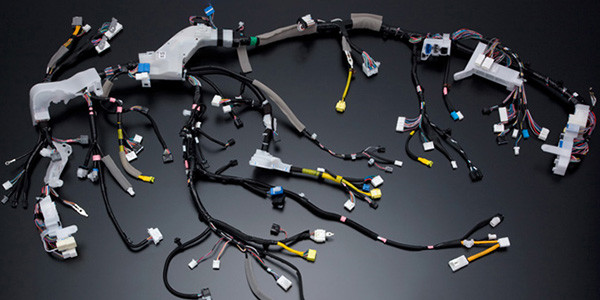
Manufacturing Process of EV Wiring Harnesses
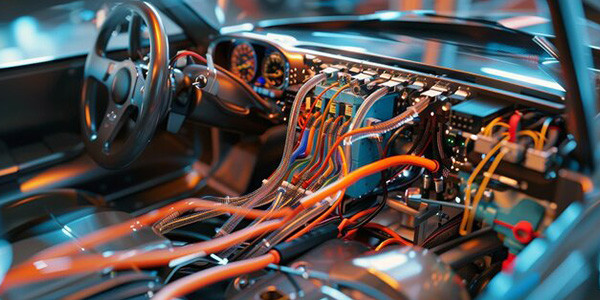
- Continuity Testing: This ensures all connections are intact, with no open circuits or broken wires. It confirms that power and signals can flow uninterrupted from one end of the harness to the other.
- High-Potential (Hi-Pot) Testing: This assesses insulation integrity by applying a high voltage (often over 1000V) to detect leaks or breakdowns. It ensures the harness can handle the electrical stresses of an EV without short-circuiting or failing.
Materials Used in EV Wiring Harnesses
The rapid evolution of electric vehicles (EVs) hinges on advanced engineering, with wiring harnesses playing a pivotal role in power distribution, signal transmission, and safety. The materials chosen for these harnesses directly impact efficiency, durability, and performance.
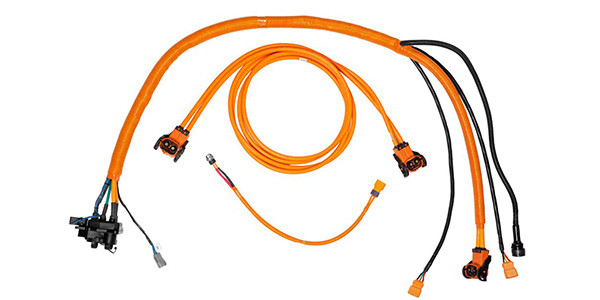
Conductors: Balancing Conductivity and Weight
Copper: The Conductivity Champion
Copper remains the gold standard for conductive materials due to its exceptional electrical conductivity (approximately 58.0 MS/m at 20°C). Its low resistance minimizes energy loss, making it ideal for high-voltage applications like battery-to-motor connections and fast-charging systems. For instance, Tesla’s Model S employs copper in its powertrain wiring to handle currents exceeding 300A. However, copper’s density (8.96 g/cm³) adds weight, prompting engineers to seek alternatives for weight-sensitive components.
Aluminum: Lightweight but Less Efficient
Aluminum, with 61% of copper’s conductivity but only 30% of its weight (2.7 g/cm³), is increasingly used in non-critical pathways. BMW’s i3, for example, integrates aluminum harnesses in auxiliary systems to reduce overall vehicle mass. The trade-offs include higher resistivity, requiring thicker wires, and susceptibility to oxidation. Manufacturers address oxidation via conductive coatings or antioxidant pastes. Despite these challenges, aluminum’s cost-effectiveness and sustainability (it’s 100% recyclable) make it attractive for mid-voltage applications like HVAC systems.
Insulation: Tailoring Materials to Voltage and Heat Demands
Low-Voltage Insulation: PVC and XLPE
For low-voltage circuits (<60V), such as infotainment or lighting, polyvinyl chloride (PVC) dominates due to its flexibility, affordability, and decent temperature range (-40°C to 105°C). Cross-linked polyethylene (XLPE), with superior thermal resistance (up to 150°C) and mechanical strength, is preferred for underhood applications near heat sources. Nissan’s Leaf uses XLPE in its battery management system (BMS) wiring to endure engine bay temperatures. However, both materials struggle with high-voltage demands, where dielectric strength becomes critical.
High-Voltage Insulation: Silicone and Fluoropolymers
High-voltage systems (300–800V) demand materials like silicone rubber and fluoropolymers (e.g., PTFE, FEP). Silicone offers unparalleled flexibility and operates reliably from -55°C to 200°C, making it ideal for battery pack interconnects in vehicles like the Chevrolet Bolt. Fluoropolymers add chemical resistance and minimal dielectric loss, crucial for inverter cables in Porsche’s Taycan. The downside? Silicone’s low abrasion resistance and fluoropolymers’ high cost (up to 5x PVC) complicate their adoption.
Specialized Materials: Enabling Next-Gen EV Designs
Lightweight Composites
To further reduce mass, automakers are adopting composites like polyether ether ketone (PEEK) and fiber-reinforced polymers. PEEK’s high strength-to-weight ratio and thermal stability (melting point: 343°C) suit it for exposed harnesses in Lucid Air’s roof-mounted LiDAR systems. These materials also resist automotive fluids, reducing maintenance costs.
High-Dielectric Insulators
As EVs push voltage limits, materials like ceramic-coated insulators and ethylene tetrafluoroethylene (ETFE) prevent electrical leakage. ETFE, with a dielectric strength of 80–160 kV/mm, is used in Rivian’s 800V charging ports to prevent arcing. Such innovations are vital for extending range and ensuring safety in humid or dusty environments.
Trade-Offs and Design Considerations
Material selection involves balancing multiple factors:
Cost vs. Performance: Copper outperforms aluminum but increases costs by 20–30%.
Weight vs. Durability: Composites save weight but may require protective sheathing.
Thermal Management: Silicone insulates well but may need additional cooling in tight spaces.
Regulatory standards also shape choices. For example, UL 1446 mandates flame-retardant insulation for battery cables, steering manufacturers toward halogen-free materials like polyolefins.
Future Trends: Innovation on the Horizon
Emerging materials aim to resolve existing compromises:
Graphene-Enhanced Conductors: Promising 40% higher conductivity than copper, potentially revolutionizing high-current pathways.
Self-Healing Insulators: Polymers that repair minor cracks autonomously could extend harness lifespan.
Bio-Based Plastics: Toyota is experimenting with plant-derived insulators to reduce carbon footprints.
Additionally, solid-state wiring systems could replace traditional harnesses, though commercialization remains years away.
Innovations and Future Trends in EV Wiring Harnesses
The electric vehicle (EV) revolution is accelerating, driven by advancements in battery technology, autonomous systems, and energy efficiency. At the heart of this transformation lies an often-overlooked component: the wiring harness. Serving as the vehicle’s central nervous system, wiring harnesses transmit power and data across an EV’s complex architecture. As automakers push for lighter, faster, and smarter vehicles, innovations in wiring harness design are becoming critical.
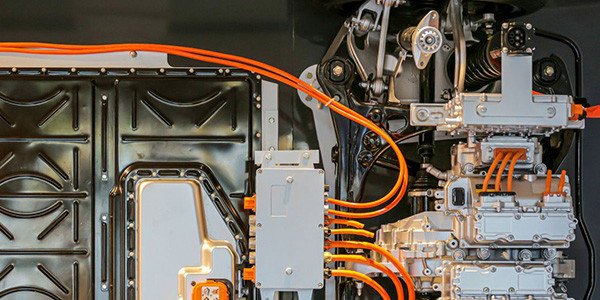
Lightweight Materials: The Pursuit of Efficiency
Carbon Fiber-Reinforced Polymers (CFRP)
Traditional copper wiring, while highly conductive, contributes significantly to vehicle weight. To address this, automakers are turning to carbon fiber composites for structural and shielding components. BMW’s iX SUV, for example, uses CFRP-reinmented cable conduits in its high-voltage harnesses, reducing weight by 30% compared to aluminum enclosures. CFRP’s high strength-to-weight ratio also improves crash safety, a key concern in battery-packed EVs.
Advanced Thermoplastics and Polymers
Materials like polyamide (PA) and polyphthalamide (PPA) are replacing conventional PVC insulation. These polymers withstand higher temperatures (up to 200°C) while being 40% lighter. Tesla’s Cybertruck employs PA-insulated cables in its 800V battery system to endure extreme thermal loads during fast charging. Emerging research from MIT highlights “conductive polymers” embedded with silver nanoparticles, which could merge insulation and conductivity into a single layer, eliminating separate shielding.
Graphene and Nanocomposites
Graphene, a single-layer carbon lattice, is being tested as a coating for aluminum wires to enhance conductivity while retaining weight savings. Startups like NanoGraf report a 25% reduction in resistive losses in prototype graphene-aluminum harnesses. Similarly, BASF’s Ultramid® Advanced N nanocomposites integrate clay nanoparticles for improved flame resistance, critical for battery proximity applications.
Smart Integration: From Power Cables to Data Highways
CAN Bus to Ethernet: The Speed Revolution
Legacy Controller Area Network (CAN) systems, limited to 1 Mbps, are struggling to support real-time data from cameras, LiDAR, and over-the-air (OTA) updates. Automotive Ethernet, operating at 10 Gbps, is emerging as the backbone for next-gen EVs. Porsche’s Taycan uses Ethernet-based harnesses to connect its ADAS (Advanced Driver Assistance Systems), enabling millisecond response times for collision avoidance.
Optical Fiber Integration
For weight-sensitive, high-bandwidth applications, automakers are embedding optical fibers into wiring harnesses. Toyota’s e-Palette concept vehicle uses fiber-optic cables to transmit data from 360-degree sensors, reducing harness weight by 50% versus copper alternatives. Researchers at Stanford are developing hybrid harnesses that combine optical fibers for data and aluminum for power, optimizing both speed and efficiency.
Wireless and Self-Diagnosing Systems
Wireless harness technology, though nascent, promises to eliminate physical cables for low-power sensors. Honda’s 2023 R&D roadmap includes Bluetooth Low Energy (BLE)-enabled pressure sensors in tires, communicating wirelessly with the central ECU. Meanwhile, “smart” harnesses with embedded microchips, like those in Rivian’s R1T, monitor insulation integrity and predict failures using AI algorithms.
Manufacturing Advances: Precision at Scale
3D Printing and Customization
Additive manufacturing is revolutionizing prototyping and low-volume production. German supplier Leoni has adopted 3D-printed harness brackets that conform to irregular spaces in EVs, reducing material waste by 70%. Similarly, startup Jabil uses AI-driven design software to create topology-optimized harness layouts, shortening development cycles from weeks to days.
Automated Robotic Assembly
Traditional harness manufacturing relies on manual labor, but companies like Aptiv and Yazaki are deploying collaborative robots (cobots) for tasks like wire cutting and connector assembly. Tesla’s Gigafactory Berlin employs a fully automated harness line where robots install 5,000 wires per hour with sub-millimeter precision, cutting labor costs by 40%.
Modular and Plug-and-Play Systems
To simplify repairs and upgrades, suppliers like TE Connectivity are designing modular harnesses with standardized connectors. Volkswagen’s MEB platform uses “plug-and-play” harness segments, allowing dealers to replace faulty sections without dismantling the entire vehicle. This approach aligns with the EU’s proposed “Right to Repair” legislation, reducing e-waste.
Emerging Research and Industry Collaborations
Solid-State Wiring Systems
Researchers at Fraunhofer Institute are experimenting with solid-state circuits printed onto flexible substrates, potentially replacing traditional wires. Early prototypes show 60% weight savings and immunity to electromagnetic interference (EMI), a major hurdle in autonomous EVs.
Self-Healing Materials
IBM’s “Voltron” project explores polymers that autonomously repair minor cracks using heat from the vehicle’s operation. Such materials could extend harness lifespan beyond the vehicle’s 15-year average, aligning with circular economy goals.
AI-Optimized Thermal Management
Startup Zunum Aero, backed by Boeing, uses machine learning to simulate heat distribution in harnesses, enabling dynamic rerouting of power during overheating. This innovation is critical for aviation-inspired EVs aiming for ultra-fast charging.
Sustainability: The Overarching Imperative
Beyond performance, the industry is prioritizing eco-friendly materials and processes. Renault’s “Re-Factory” initiative recycles 95% of harness copper from end-of-life EVs, while Henkel’s Loctite® conductive adhesives eliminate solder, reducing lead usage.
Conclusion: Wiring the Future
The EV wiring harness is evolving from a passive component to an intelligent, multi-functional system. Innovations in lightweight composites, high-speed data integration, and automated manufacturing are not just enhancing performance—they’re redefining what’s possible in electric mobility. As solid-state technologies and AI-driven designs mature, the humble wiring harness will play a starring role in achieving lighter, faster, and truly sustainable transportation.