Blogs & News
We are focus on automotive wiring harness & connectors technology.
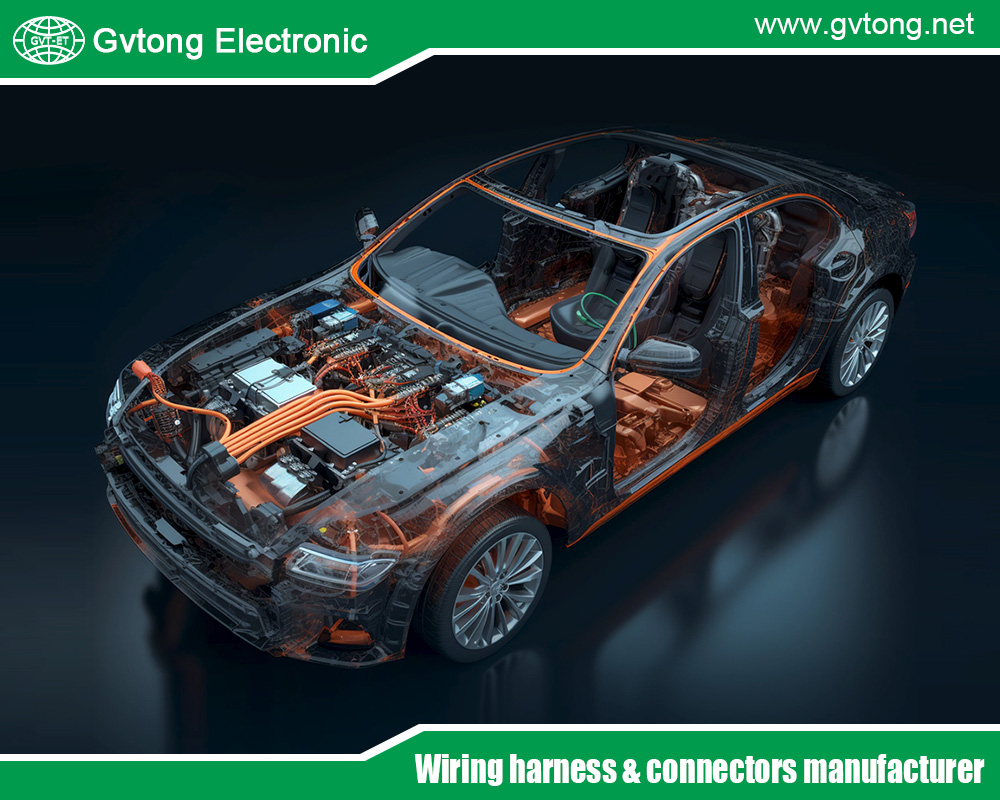
New Direction of Automotive Development: In-Depth Analysis of Three-Cavity Connectors
- Gvtong Electronic
- 10-cavity connectors, 2-cavity connectors company, 3-cavity connectors manufacturer, 4-cavity connectors supplier, 48V board net connectors, 5-cavity connectors system, 6-cavity connector, 7-cavity connectors system, 8-cavity connector market, 8-cavity connector technology, 9-cavity connectors market, ADAS sensor connectors, Automated assembly connectors, Automotive data connectorAutomotive power distribution connector, automotive diagnostic connector, automotive high - frequency, automotive hybrid connector, automotive optical fiber connector, automotive vibration - resistant, Automotive-grade AEC-Q200 connectors, Battery management system (BMS) connectors, best three-cavity connectors, EV charging connectors, Fuel cell connectors, Halogen-free automotive connectors, In-cabin infotainment connectors, Lightweight automotive connectors, OEM-specific connectors, Pre-charge/discharge connectors, Quick-fit automotive connectors, Recyclable material connectors, Redundant safety connectors, Thermal management connectors, three-cavity connectors, three-cavity connectors manufacturer, three-cavity connectors supplier, V2X communication connectors, Wireless charging connectors
- No Comments
New Direction of Automotive Development: In-Depth Analysis of Three-Cavity Connectors
The automotive industry is undergoing a transformative phase, driven by electrification, autonomous driving, and advanced connectivity. As vehicles evolve into sophisticated systems integrating electronics, software, and mechanical components, the demand for reliable, efficient, and compact electrical connectors has surged. Among these, three-cavity connectors have emerged as critical components, enabling robust electrical interfaces in modern vehicles. These connectors, designed to house three electrical terminals, are integral to automotive wiring harnesses, supporting applications from power distribution to sensor integration. This article provides an in-depth analysis of three-cavity connectors, exploring their design, functionality, and role in shaping the future of automotive development. By examining their technical specifications, applications, and alignment with industry trends, we aim to highlight their significance in the rapidly evolving automotive landscape. As vehicles become more electrified and connected, understanding the role of such components offers insights into the engineering challenges and innovations driving the industry forward.
The Evolution of Automotive Electrical Systems
The automotive industry has shifted from mechanical-centric designs to complex electrical and electronic architectures. In the early 20th century, vehicles relied on basic wiring for ignition and lighting. Today, electric vehicles (EVs), hybrid electric vehicles (HEVs), and autonomous vehicles demand intricate electrical systems to support high-voltage batteries, advanced driver-assistance systems (ADAS), and vehicle-to-everything (V2X) communication. According to industry reports, modern vehicles can contain up to 3,000 meters of wiring and hundreds of connectors, reflecting the growing complexity of automotive electronics.
Three-cavity connectors have become essential in this context due to their versatility and reliability. These connectors typically house three electrical terminals, facilitating connections for power, ground, and signal lines in a single compact unit. Their design supports the integration of sensors, actuators, and control modules, which are critical for functions like battery management, thermal regulation, and infotainment systems. As vehicles transition to 48-volt architectures and high-voltage EV systems, connectors must withstand higher currents, temperatures, and environmental stresses. Three-cavity connectors, with their standardized yet adaptable designs, meet these demands while maintaining cost-effectiveness and ease of assembly.
The rise of software-defined vehicles further amplifies the importance of connectors. With over-the-air (OTA) updates and real-time data processing, connectors must ensure stable, low-latency communication. Three-cavity connectors, often used in CAN (Controller Area Network) bus systems, enable reliable data transmission, making them indispensable in modern automotive designs.
Technical Specifications of Three-Cavity Connectors
Three-cavity connectors are engineered to meet stringent automotive requirements, balancing performance, durability, and compactness. Typically, these connectors consist of a housing, terminals, seals, and locking mechanisms. The housing, made from high-grade thermoplastics like polyamide or PBT, provides insulation and resistance to heat, vibration, and chemicals. The terminals, usually copper or brass with tin or gold plating, ensure low contact resistance and high conductivity. Seals, often silicone-based, protect against moisture, dust, and corrosion, achieving IP67 or higher ingress protection ratings.
The connectors are designed to handle a range of electrical loads, from low-current signals (e.g., 1-5A for sensors) to moderate power applications (up to 20A for actuators). Their three-cavity configuration typically supports a power line, ground, and signal or data line, making them ideal for applications like oxygen sensors, fuel injectors, or lighting modules. The connectors often comply with standards like ISO 16750 (environmental conditions for electrical equipment) and USCAR specifications, ensuring compatibility across global automotive platforms.
Locking mechanisms, such as positive latch systems, prevent accidental disconnection under vibration, a common challenge in automotive environments. Additionally, three-cavity connectors are designed for high mating cycles (often exceeding 50 cycles), ensuring longevity in applications requiring frequent maintenance. Their compact size, typically 20-30 mm in length, allows integration into tight spaces, a critical factor in densely packed vehicle architectures.
Manufacturers like TE Connectivity, Molex, and Aptiv offer three-cavity connectors with variations like sealed or unsealed designs, depending on the application. For instance, sealed connectors are used in under-hood environments, while unsealed versions suffice for interior applications. Advanced versions incorporate features like terminal position assurance (TPA) to prevent misalignment and ensure secure connections.
Applications in Modern Vehicles
Three-cavity connectors are ubiquitous in modern vehicles, supporting a wide range of systems critical to performance, safety, and user experience. In electric vehicles, they are used in battery management systems (BMS) to connect sensors monitoring voltage, temperature, and state of charge. For example, a three-cavity connector might link a temperature sensor to the BMS, ensuring safe operation of high-voltage batteries.
In internal combustion engine (ICE) vehicles, these connectors are common in engine control units (ECUs), facilitating connections for fuel injectors, throttle position sensors, and ignition coils. Their ability to handle moderate currents and resist harsh conditions like heat and oil exposure makes them ideal for under-hood applications.
Autonomous vehicles rely heavily on sensors and cameras, many of which use three-cavity connectors for power and data transmission. For instance, LIDAR and radar systems, critical for ADAS, often employ these connectors to ensure reliable communication with the vehicle’s central processor. Similarly, in infotainment systems, three-cavity connectors support interfaces for microphones, speakers, or USB ports, enabling seamless connectivity for passengers.
The rise of V2X communication, which allows vehicles to interact with infrastructure and other vehicles, further underscores the importance of three-cavity connectors. These connectors facilitate CAN or LIN (Local Interconnect Network) bus connections, enabling real-time data exchange for features like traffic signal prioritization or collision avoidance.
In hybrid vehicles, three-cavity connectors bridge high-voltage and low-voltage systems, ensuring safe and efficient power distribution. Their versatility also extends to lighting systems, where they connect LED modules or headlamp controls, contributing to energy efficiency and design flexibility.
Alignment with Automotive Trends
The automotive industry is pivoting toward electrification, autonomy, and connectivity, and three-cavity connectors are well-positioned to support these trends. Electrification, driven by global emission regulations, has increased demand for connectors that can handle high-voltage and high-current applications. While three-cavity connectors are typically used for low- to medium-power applications, their role in auxiliary systems like cooling pumps or battery sensors remains critical. Their compact design aligns with the industry’s push for lightweight components to improve EV range.
Autonomous driving relies on a network of sensors, cameras, and processors, all requiring reliable electrical connections. Three-cavity connectors support the high-speed data transmission needed for real-time decision-making, particularly in CAN or Ethernet-based systems. As vehicles move toward Level 4 and 5 autonomy, the number of connectors per vehicle is expected to increase, with three-cavity designs offering a balance of performance and cost.
Connectivity, including 5G integration and OTA updates, demands robust data pathways. Three-cavity connectors, often used in communication modules, ensure low-latency, error-free data transfer. Their standardized designs also facilitate scalability, allowing manufacturers to integrate them across various vehicle platforms.
Sustainability is another key trend influencing connector design. Manufacturers are exploring recyclable materials and modular designs to reduce waste. Three-cavity connectors, with their standardized footprints, support modular wiring harnesses, enabling easier repairs and upgrades. Additionally, their durability reduces the need for frequent replacements, aligning with circular economy principles.
Challenges and Innovations
Despite their advantages, three-cavity connectors face challenges in meeting the demands of next-generation vehicles. The shift to high-voltage systems (e.g., 800V for fast-charging EVs) requires connectors with enhanced insulation and thermal management. While three-cavity connectors are primarily designed for lower-power applications, innovations like advanced dielectric materials and cooling channels are expanding their capabilities.
Miniaturization is another challenge. As vehicles incorporate more electronics, space constraints intensify. Manufacturers are developing ultra-compact three-cavity connectors without compromising performance, using techniques like micro-molding and high-density terminal designs.
Reliability under extreme conditions remains critical. Automotive connectors must withstand temperatures from -40°C to 125°C, vibrations, and chemical exposure. Innovations like anti-vibration locks and corrosion-resistant coatings are addressing these challenges, ensuring three-cavity connectors meet rigorous standards.
The rise of smart manufacturing is also influencing connector production. Automated assembly lines and AI-driven quality control are improving precision and reducing costs. For instance, Molex has introduced connectors with integrated diagnostics, allowing real-time monitoring of connection integrity, which enhances reliability in autonomous vehicles.
Future Directions and Industry Impact
Looking ahead, three-cavity connectors will continue to play a pivotal role in automotive development. The transition to fully electric and autonomous vehicles will drive demand for connectors that support higher data rates and power levels. Emerging standards like Automotive Ethernet and 800V architectures will push manufacturers to innovate, potentially integrating features like shielding for electromagnetic compatibility (EMC) into three-cavity designs.
The adoption of solid-state batteries, expected to enter mass production by 2030, will require connectors with enhanced thermal and electrical performance. Three-cavity connectors could evolve to support these systems, particularly in auxiliary circuits. Additionally, the growth of shared mobility and vehicle-to-grid (V2G) systems will increase the need for durable, high-cycle connectors to support frequent charging and discharging.
The global automotive connector market, valued at approximately $15 billion in 2023, is projected to grow at a CAGR of 6% through 2030, driven by EV adoption and ADAS proliferation. Three-cavity connectors, due to their versatility and cost-effectiveness, will remain a key segment of this market.
Collaboration between automakers and connector manufacturers will be crucial. Companies like Aptiv and TE Connectivity are partnering with OEMs to develop custom solutions, ensuring connectors meet specific vehicle requirements. Open standards and modular designs will further enhance the adoption of three-cavity connectors across diverse platforms.
Conclusion
Three-cavity connectors may seem like small components, but their impact on automotive development is profound. As vehicles become more electrified, autonomous, and connected, these connectors provide the reliability, versatility, and efficiency needed to support complex electrical systems. Their ability to handle power, signal, and data transmission in a compact, durable package makes them indispensable in applications ranging from battery management to ADAS. Despite challenges like miniaturization and high-voltage demands, ongoing innovations in materials, design, and manufacturing are ensuring their relevance in the future of mobility. As the automotive industry embraces trends like sustainability and smart connectivity, three-cavity connectors will continue to evolve, supporting the seamless integration of advanced technologies. By enabling robust electrical interfaces, these connectors are not just keeping pace with automotive progress but are actively shaping its direction, proving that even the smallest components can drive significant change.
For more about the new direction of automotive development: in-depth analysis of three-cavity connectors, you can pay a visit to Gvtong at https://www.gvtong.net/ for more info.
Recent Posts
Tips for Selecting Heat-Resistant Wiring in Vehicle Hot Spots
Detecting & Fixing Loose or Faulty Connections in Car Wiring
How Does a Qualified Mechanic Solve Car Electrical Problems?
Top Tips to Prevent Wear in Automotive Wiring
Why Protecting Electrical Systems from Moisture Is Critical
Tags
Recommended Products
-
Automotive RF MINI FAKRA Four-Core Connector, Quad Port, PCB Through Hole, Right Angle, Plug, 50 Ohm
-
GE Series-8-core three-row signal connector
-
Automotive Plastic Injection Parts
-
Low voltage connector-30PIN socket + plug
-
DCDC through-wall terminal – 90°180°
-
Automotive FAKRA Single Head Connector, Automotive Standard FAKRA Connectors
-
GE Series-35-core three-row signal connector
-
DCDC wall-through terminal – with protective cover