Blogs & News
We are focus on automotive wiring harness & connectors technology.
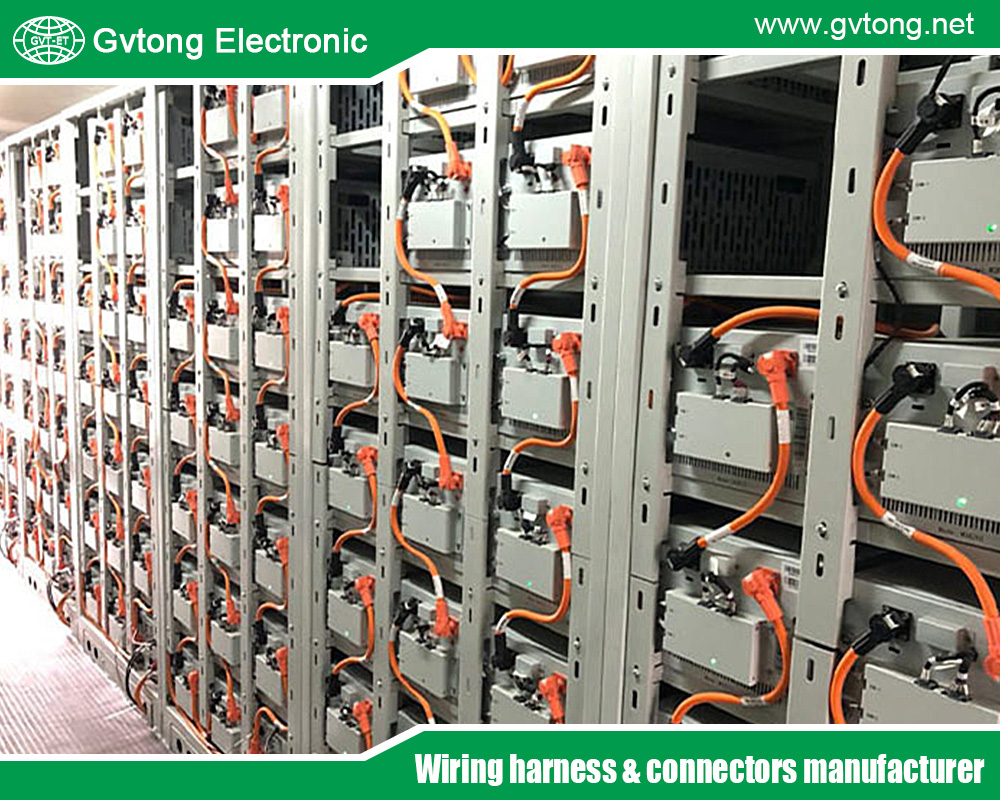
Automotive Low Voltage Waterproof Connectors: Ensuring Reliability in Harsh Environments
- Gvtong Electronic
- 48V board net connectors, Anti-vibration automotive connectors, Automated assembly connectors, automotive diagnostic connector, automotive electrical connector, automotive High voltage connector, automotive hybrid connector, automotive Low voltage connector, automotive low voltage waterproof connectors, automotive low voltage waterproof connectors factory, automotive low voltage waterproof connectors manufacturer, automotive low voltage waterproof connectors supplier, automotive Oil-resistant Connectors, Automotive power distribution connector, Automotive shielded connectors, automotive Signal Connector, Automotive temperature - resistant connector, automotive waterproof connectors, Automotive-grade AEC-Q200 connectors, best automotive low voltage waterproof connectors, Cost-effective automotive connectors, Halogen-free automotive connectors, High-speed data connectors, High-temperature resistant connectors, low voltage waterproof connectors, Low Voltage Waterproof Connectors Manufacturer China, Multi-variation connectors, Oil-resistant automotive connectors, Recyclable material connectors, Redundant safety connectors, Thermal management connectors, Wireless charging connectors
- No Comments
Automotive Low Voltage Waterproof Connectors: Ensuring Reliability in Harsh Environments
In the intricate world of modern vehicles, electrical connectors are the unsung heroes that keep systems running smoothly. Among these, low voltage waterproof connectors stand out as critical components, designed to maintain reliable electrical connections in the face of water, dust, and other environmental challenges. Operating typically at voltages below 60V DC, these connectors are vital for powering and communicating with systems like lighting, sensors, and infotainment in cars, trucks, and electric vehicles (EVs). As vehicles become more electrified, connected, and autonomous, the demand for robust, waterproof connectors grows, ensuring performance and safety in even the harshest conditions.
This article provides an in-depth exploration of automotive low voltage waterproof connectors, covering their definition, types, applications, design considerations, challenges, and emerging trends. By understanding their role and evolution, we gain insight into how these small but mighty components drive the reliability and innovation of modern automotive systems.
What Are Low Voltage Waterproof Connectors?
Low voltage waterproof connectors are specialized electrical connectors engineered to transmit power and signals in automotive systems while resisting ingress from water, dust, and other contaminants. These connectors typically operate at voltages up to 60V DC, distinguishing them from high-voltage connectors used in EV powertrains. Their waterproofing capability is critical in automotive environments, where exposure to rain, road spray, and cleaning fluids is commonplace.
Key Features
- Ingress Protection (IP) Ratings: Waterproof connectors are rated using the IP standard (e.g., IP67, IP68), indicating their resistance to dust and water. For instance, IP67 connectors can withstand submersion in 1 meter of water for 30 minutes.
- Low Voltage Operation: Designed for systems requiring low current and voltage, such as sensors or lighting, typically below 60V DC.
- Durability: Built to endure vibrations, temperature extremes, and chemical exposure.
Importance in Vehicles
Waterproof connectors ensure that critical systems—such as advanced driver assistance systems (ADAS), exterior lighting, and engine sensors—function reliably, even in adverse conditions. A failure in these connectors could lead to system malfunctions, compromising safety or performance. Their role is especially crucial in off-road vehicles, EVs, and regions with extreme weather.
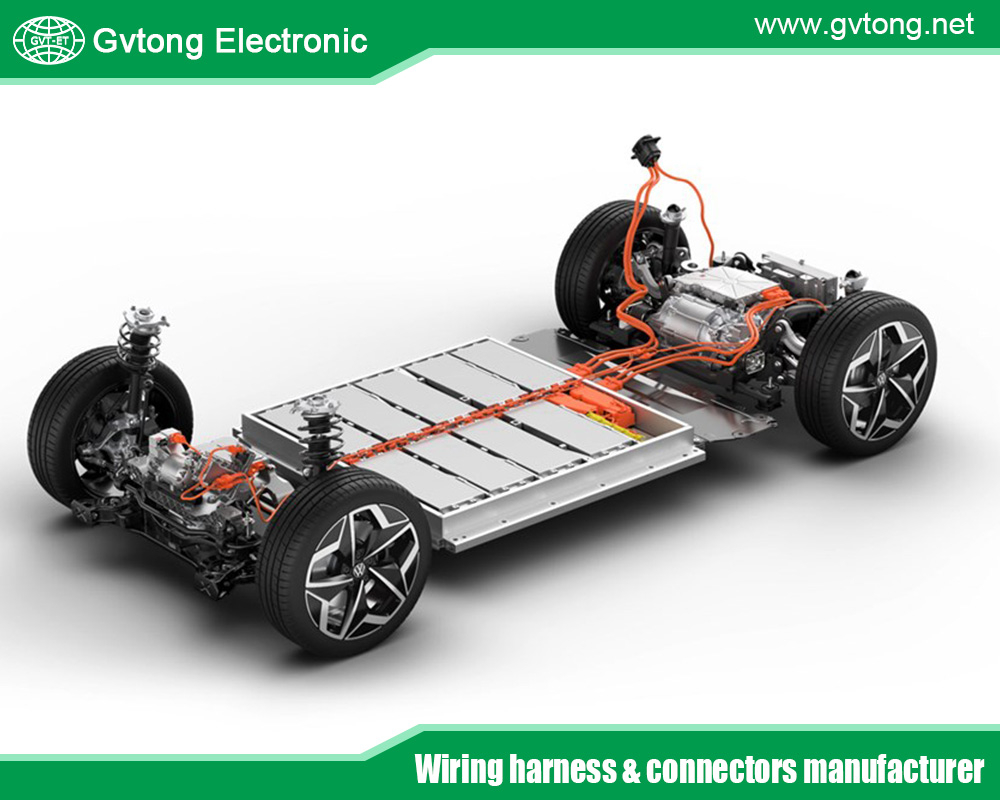
Types of Low Voltage Waterproof Connectors
Several types of low voltage waterproof connectors are used in automotive applications, each tailored to specific needs and environments:
Pin and Socket Connectors
These connectors feature a male pin that inserts into a female socket, sealed with gaskets or O-rings to prevent water ingress. They are versatile and commonly used for sensor connections and wiring harnesses, offering easy assembly and reliable sealing.
Circular Connectors
Circular connectors, often with threaded or bayonet locking mechanisms, provide robust sealing for harsh environments. They are ideal for exterior applications like lighting or cameras, where exposure to water and dust is frequent.
Rectangular Connectors
Rectangular waterproof connectors are used in space-constrained areas, such as interior modules or engine compartments. Their compact design and high pin density make them suitable for multi-signal applications.
Coaxial Waterproof Connectors
For high-frequency signals, such as those in telematics or radar systems, coaxial waterproof connectors offer shielding and sealing to maintain signal integrity in wet conditions.
Materials
- Contacts: Typically made from copper alloys (e.g., brass or phosphor bronze) with gold or tin plating for corrosion resistance.
- Housings: Constructed from durable plastics like polyamide or PBT, resistant to chemicals and UV exposure.
- Seals: Silicone or rubber gaskets ensure watertight connections.
Applications in Modern Vehicles
Low voltage waterproof connectors are deployed across various vehicle domains, each with unique environmental challenges.
Exterior Systems
Exterior connectors face constant exposure to weather:
- Lighting: Headlights, taillights, and fog lights rely on waterproof connectors to maintain functionality in rain or snow.
- Sensors: ADAS components, such as radar and ultrasonic sensors, use waterproof connectors to transmit data reliably, even during heavy downpours.
Engine Compartment
In the engine bay, connectors link sensors, actuators, and ECUs for functions like fuel injection and emissions control. They must resist not only water but also high temperatures, oil, and vibrations.
Interior Systems
While interiors are less exposed to water, waterproof connectors are used in areas prone to spills or humidity, such as door modules (for power windows and locks) or climate control systems.
Electric and Hybrid Vehicles
EVs and hybrids require waterproof connectors for low-voltage systems like battery management, charging interfaces, and auxiliary electronics. These connectors ensure safety and reliability in wet conditions.
Specific Examples
- Parking Assistance Systems: Ultrasonic sensors in bumpers use waterproof connectors to communicate with ECUs, unaffected by rain or car washes.
- Telematics Modules: Waterproof coaxial connectors support vehicle-to-everything (V2X) communication, enabling real-time data exchange.
Design Considerations
Designing low voltage waterproof connectors for automotive use involves addressing several critical factors to ensure performance and longevity.
Ingress Protection
Achieving high IP ratings requires precise engineering:
- Sealing Mechanisms: Gaskets, O-rings, or overmolded designs block water and dust.
- Locking Systems: Threaded or snap-lock mechanisms ensure connectors stay sealed under vibration.
Environmental Resistance
Connectors must withstand:
- Temperature Extremes: From -40°C to over 125°C in engine compartments.
- Chemical Exposure: Resistance to oils, fuels, and road salts.
- UV Exposure: For exterior connectors, UV-resistant materials prevent degradation.
Electrical Performance
- Contact Resistance: Low resistance minimizes signal loss, achieved with high-quality, corrosion-resistant contacts.
- Current Capacity: Connectors must handle the required current without overheating, even in sealed designs.
Mechanical Durability
- Vibration Resistance: Locking mechanisms and robust housings prevent disconnection.
- Mating Cycles: Connectors must endure repeated connections (e.g., during maintenance) without losing sealing or performance.
Standards and Testing
Automotive connectors comply with standards from organizations like SAE, ISO, and IEC. Testing includes:
- Water Immersion: To verify IP ratings.
- Thermal Cycling: To ensure performance across temperature ranges.
- Salt Spray: To assess corrosion resistance.
Challenges in Waterproof Connector Design
Despite their importance, designing low voltage waterproof connectors presents several challenges:
Achieving High IP Ratings
Higher IP ratings (e.g., IP68) demand tighter seals and stronger materials, increasing complexity and cost. Balancing protection with affordability is a constant challenge.
Miniaturization
As vehicles incorporate more electronics, connectors must shrink to fit tight spaces. Smaller designs risk compromising sealing or durability, requiring innovative engineering.
Corrosion
Moisture, combined with salts or chemicals, can corrode contacts over time. Gold or tin plating helps, but long-term exposure remains a concern, especially in coastal regions.
Thermal Management
Sealed connectors trap heat, potentially affecting performance. Designers must optimize heat dissipation while maintaining waterproofing.
Cost Pressures
Automakers seek cost-effective solutions without sacrificing quality. This drives the use of economical materials and streamlined manufacturing processes that still meet rigorous standards.
Solutions and Innovations
- Advanced Sealing: Overmolding and ultrasonic welding create seamless, watertight housings.
- Hybrid Designs: Combining power and signal in one connector reduces the number needed, saving space and cost.
- Corrosion-Resistant Alloys: New coatings improve longevity in harsh environments.
Future Trends
The future of low voltage waterproof connectors is shaped by automotive advancements and technological innovations.
Electrification
EVs and hybrids increase the need for waterproof connectors in low-voltage systems, such as battery monitoring and charging. Lightweight materials like composites reduce vehicle weight, boosting efficiency.
Autonomous Vehicles
Self-driving cars rely on sensors and cameras, all requiring waterproof connectors to function in rain or snow. These connectors must support higher data rates for real-time processing.
Smart Connectors
Future connectors may embed sensors to monitor sealing integrity or environmental exposure, enabling predictive maintenance to prevent failures.
Sustainable Materials
With sustainability goals, manufacturers are exploring recyclable plastics and eco-friendly coatings to reduce environmental impact.
High-Speed Data
As vehicles adopt Ethernet and 5G, waterproof connectors must handle high-frequency signals without compromising IP ratings, using advanced shielding and materials.
Wireless Alternatives
While wireless tech reduces some connector needs, critical systems still require physical connections for reliability, ensuring waterproof connectors remain essential.
Case Studies and Real-World Impact
- Off-Road Vehicles: Brands like Land Rover use IP68-rated connectors for sensors in their SUVs, enabling river crossings without electrical failures.
- EVs in Wet Climates: Tesla’s low-voltage connectors in models like the Model 3 ensure battery management systems operate reliably in rainy regions.
- Motorsport: In Formula E, waterproof connectors withstand high-speed, wet conditions, supporting sensors and telemetry.
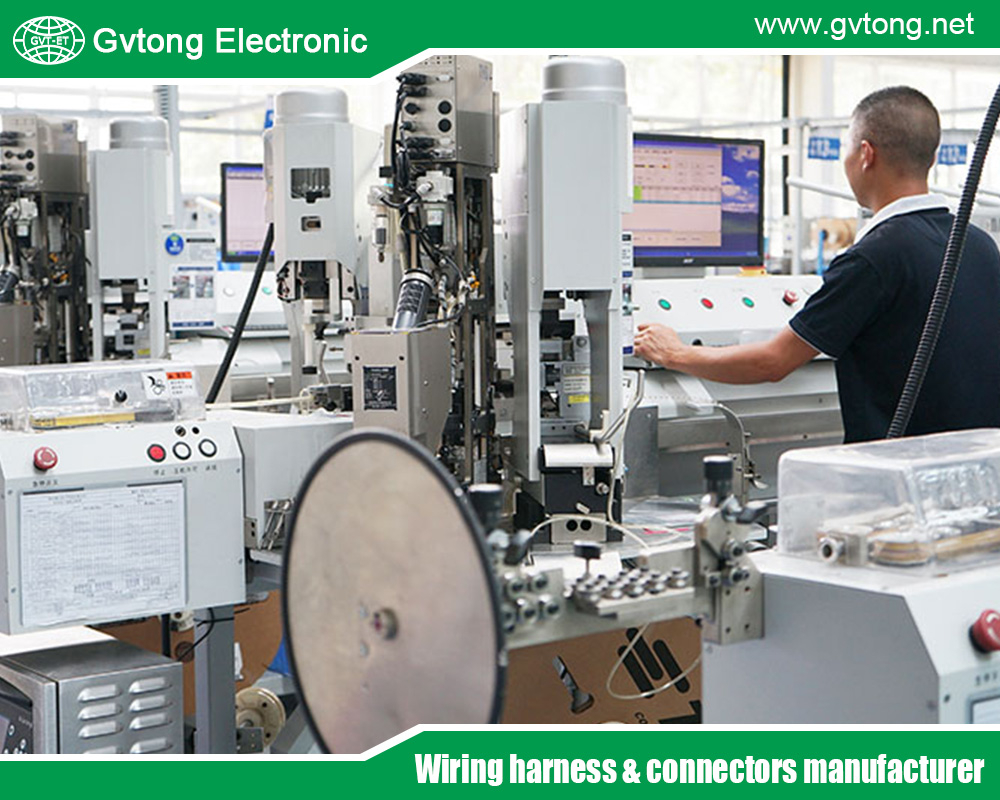
Conclusion
Automotive low-voltage waterproof connectors are the silent guardians of vehicle reliability, ensuring electrical systems perform flawlessly despite rain, dust, or extreme conditions. Their design is a delicate balance of sealing, durability, and electrical performance, meeting stringent automotive standards. Challenges like corrosion, miniaturization, and cost drive continuous innovation, from advanced materials to smart features. As vehicles evolve toward electrification, autonomy, and connectivity, these connectors will play an even bigger role, adapting to higher data demands, and greener technologies.
Next time you drive through a storm or power on your car’s sensors, remember the low voltage waterproof connectors working tirelessly behind the scenes. They’re small, but their impact on safety, performance is enormous, making them a cornerstone of the automotive future.
For more about the best automotive low voltage waterproof connectors: ensuring reliability in harsh environments, you can pay a visit to Gvtong at https://www.gvtong.net/ for more info.
Recent Posts
How Does a Qualified Mechanic Solve Car Electrical Problems?
Top Tips to Prevent Wear in Automotive Wiring
Why Protecting Electrical Systems from Moisture Is Critical
Automotive Diagnostic Connectors: The Gateway to Vehicle Health
Tips on How to Reduce Failure-Inducing Wear in Automotive Wiring
Tags
Recommended Products
-
Energy storage connector 10.0mm
-
GE Series-48-core Low Voltage Connector-Socket+Plug
-
H630 Series-3-core plastic high voltage connector
-
GD Series – Combined Power Connector – (2+1+5) Cores
-
GE Series-8-core Rotary Signal Connector
-
GF Series-2+12 Floating Connector
-
Five-in-one terminal
-
GE double row 40pin signal connector socket