Blogs & News
We are focus on automotive wiring harness & connectors technology.
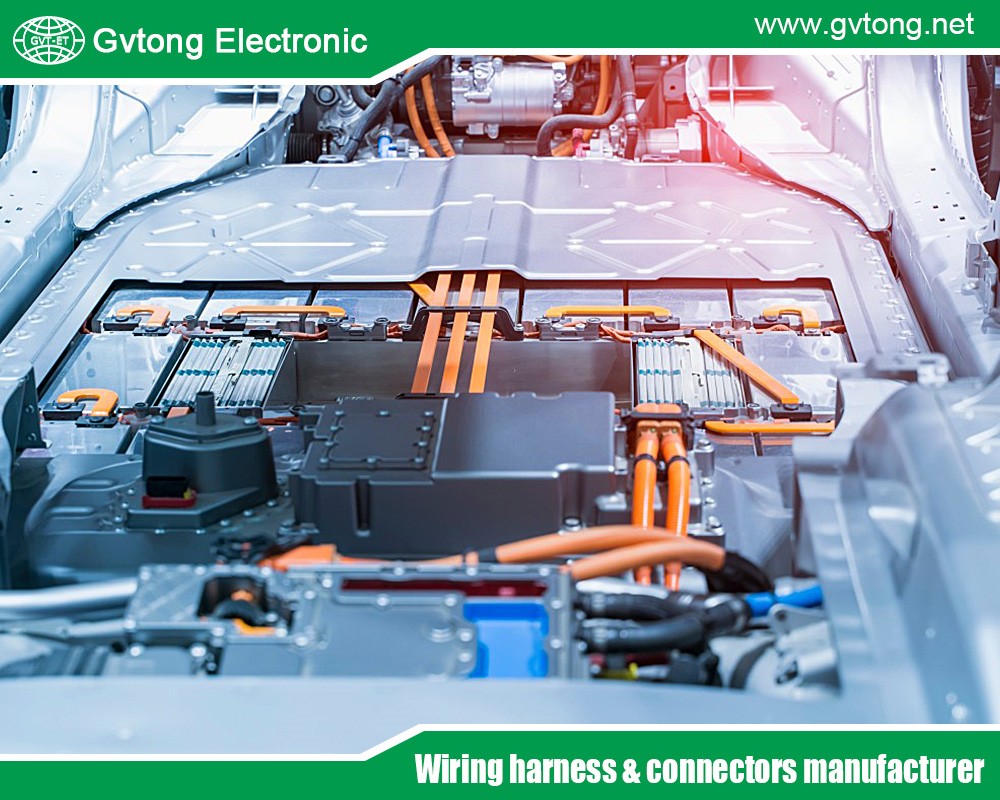
How to Choose the Suitable 2-Cavity Connector for a Project
- Gvtong Electronic
- 10-cavity connectors factory, 2 pin waterproof electrical connector, 2-cavity connectors, 2-cavity connectors manufacturer, 2-cavity connectors supplier, 4-cavity connectors, Anti-vibration automotive connectors, automotive antenna connector, automotive coaxial connector, automotive data connector, automotive electrical connector, automotive High voltage connector, automotive Low voltage connector, automotive Oil-resistant Connectors, Automotive shielded connectors, automotive waterproof connectors, Battery management system (BMS) connectors, Blind-mate automotive connectors, EV charging connectors, Fuel cell connectors, High-speed data connectors, High-temperature resistant connectors, In-cabin infotainment connectors, Lightweight automotive connectors, Low-contact resistance connectors, Modular automotive connectors, OEM-specific connectors, Oil-resistant automotive connectors, Pre-charge/discharge connectors, Quick-fit automotive connectors, V2X communication connectors
- No Comments
How to Choose the Suitable 2-Cavity Connector for a Project
In the rapidly evolving world of automotive and industrial design, selecting the right electrical connector is critical to ensuring project success. 2-cavity connectors, designed to house two electrical terminals, are widely used in applications requiring compact, reliable connections for power, ground, or signal transmission. From automotive wiring harnesses to industrial control systems, these connectors offer simplicity and efficiency, making them a popular choice for projects with constrained space or budget. However, choosing a suitable 2-cavity connector involves navigating a complex landscape of technical specifications, environmental conditions, and application requirements. This article provides a comprehensive guide to selecting the right 2-cavity connector for your project, covering key factors such as electrical performance, environmental durability, size constraints, and compatibility with modern trends like electrification and connectivity. By understanding the technical nuances and practical considerations, engineers and project managers can make informed decisions, ensuring reliable, cost-effective, and future-proof solutions for their projects.
Understanding the Role of 2-Cavity Connectors
2-cavity connectors are compact electrical components that house two terminals, typically used for power and ground, signal and ground, or dual-signal applications. In automotive projects, they are integral to wiring harnesses, connecting components like sensors, actuators, or lighting modules. Their small size and simplicity make them ideal for applications with minimal circuit requirements, such as oxygen sensors in internal combustion engine (ICE) vehicles or temperature sensors in electric vehicles (EVs).
The role of 2-cavity connectors extends beyond automotive applications. In industrial automation, they connect proximity sensors or small motors. In consumer electronics, they support compact interfaces like USB or audio connections. Their versatility stems from their ability to handle low to moderate currents (typically 1-15A) and support data protocols like LIN (Local Interconnect Network) or analog signals.
Choosing the right 2-cavity connector requires understanding the project’s specific needs. For example, an automotive project may prioritize environmental sealing for under-hood use, while an industrial project may focus on high mating cycles for frequent maintenance. Key considerations include electrical performance, environmental conditions, size constraints, and compatibility with industry standards. By aligning the connector choice with project goals, designers can ensure reliability, cost-efficiency, and scalability.
Step 1: Define Project Requirements
The first step in selecting a 2-cavity connector is to define the project’s technical and operational requirements. This involves answering key questions about the application:
- Electrical Requirements: Determine the current and voltage the connector must handle. For example, a 2-cavity connector for an automotive sensor might need to support 1-5A at 12V, while an EV cooling pump may require up to 15A at 48V. Ensure the connector’s terminals, typically copper or brass with tin or gold plating, can handle the required load without excessive heat or resistance.
- Signal Type: Identify whether the connector will transmit power, analog signals, or digital data. For instance, a connector for a CAN bus sensor requires low contact resistance for reliable data transmission, while a power connector prioritizes high current capacity.
- Environmental Conditions: Assess the operating environment. Automotive under-hood applications demand connectors with IP67 or IP69K sealing to resist moisture, dust, and temperatures up to 125°C. Interior applications, like infotainment, may use unsealed connectors with lower environmental requirements.
- Mating Cycles: Consider how often the connector will be connected and disconnected. Maintenance-heavy applications, like industrial sensors, require connectors with high mating cycles (50-100), while permanent connections prioritize locking strength.
- Size and Space Constraints: Measure the available space. 2-cavity connectors are compact (typically 15-25 mm in length), but tight spaces may require micro or mini designs, such as Molex’s Mini-Fit Jr. or TE Connectivity’s Micro MATE-N-LOK.
- Standards Compliance: Ensure the connector meets relevant standards, such as ISO 16750 for automotive environmental testing or USCAR for connector performance. Compliance ensures compatibility with existing systems and regulatory requirements.
By documenting these requirements, you create a clear framework for evaluating connector options, avoiding costly mismatches or redesigns.
Step 2: Evaluate Connector Design Features
Once project requirements are defined, evaluate the design features of 2-cavity connectors to ensure they meet your needs. Key features include:
- Housing Material: Most 2-cavity connectors use thermoplastics like polyamide or PBT for insulation and durability. For high-temperature environments (e.g., EV battery compartments), choose connectors with heat-resistant materials like polyphenylene sulfide (PPS), which withstands up to 150°C.
- Terminal Design: Terminals should match the electrical load. Tin-plated terminals are cost-effective for low-current applications, while gold-plated terminals reduce contact resistance for signal-critical systems. Ensure terminal size (e.g., 0.64 mm or 1.5 mm) supports the wire gauge (typically 18-22 AWG for 2-cavity connectors).
- Sealing and Protection: For harsh environments, select sealed connectors with silicone gaskets or O-rings, achieving IP67 or higher ratings. Unsealed connectors suffice for interior or controlled environments but are less durable in moisture or dust exposure.
- Locking Mechanisms: Positive latches or secondary locks prevent disconnection under vibration, a common issue in automotive and industrial settings. Terminal position assurance (TPA) features ensure proper terminal alignment, reducing the risk of poor connections.
- Polarization and Keying: These features prevent incorrect mating, which is critical in complex wiring harnesses. Polarized designs ensure the connector can only be inserted in the correct orientation, reducing assembly errors.
- Shielding: For data-sensitive applications, such as Automotive Ethernet or sensor connections, choose connectors with EMI shielding to minimize interference. This is increasingly important in autonomous vehicles with dense electronic systems.
Manufacturers like Aptiv, TE Connectivity, and Yazaki offer 2-cavity connectors with these features, tailored to specific applications. For example, Aptiv’s Weather-Pack series provides robust sealing for automotive use, while TE’s Mini-Universal MATE-N-LOK is versatile for industrial projects.
Step 3: Match Connector to Application
Matching the 2-cavity connector to the specific application ensures optimal performance. Common applications include:
- Automotive Sensors: In ICE vehicles, 2-cavity connectors link sensors like oxygen or crankshaft position sensors to ECUs, requiring sealed designs and low-current terminals (1-5A). In EVs, they connect temperature or pressure sensors in BMS, demanding heat resistance and reliability.
- Lighting Systems: 2-cavity connectors support LED modules or headlamp controls, prioritizing compact size and moderate current capacity (5-10A). Unsealed connectors may suffice for interior lighting, while exterior applications require IP67 sealing.
- Industrial Automation: Proximity sensors or small actuators often use 2-cavity connectors, requiring high mating cycles and vibration resistance. For example, a connector for a factory conveyor sensor must withstand frequent maintenance and dust exposure.
- Consumer Electronics: In automotive infotainment or portable devices, 2-cavity connectors support USB or audio interfaces, emphasizing compact size and signal integrity. Gold-plated terminals are preferred for low-noise data transmission.
Consider the specific demands of the application. For instance, an EV project may require a connector compatible with 48V systems, while an industrial project may prioritize ruggedness over size. Cross-reference manufacturer datasheets to ensure the connector meets current, voltage, and environmental specifications. For example, Molex’s Mini-Fit Jr. is ideal for compact, moderate-power applications, while Yazaki’s sealed 2-cavity connectors suit harsh automotive environments.
Step 4: Consider Cost and Scalability
Cost and scalability are critical factors in connector selection. 2-cavity connectors are generally cost-effective due to their simplicity and widespread use, but variations in materials and features impact pricing. For example, sealed connectors with gold-plated terminals are more expensive than unsealed, tin-plated versions. Balance performance needs with budget constraints to avoid over-specifying.
- Material Costs: Thermoplastic housings and tin-plated terminals reduce costs for low-budget projects, while PPS or gold-plated options are pricier but necessary for high-performance applications.
- Manufacturing and Assembly: Standardized connectors, like TE Connectivity’s Mini MATE-N-LOK, streamline assembly due to their compatibility with automated processes, reducing labor costs. Custom connectors may increase expenses but are justified for specialized projects.
- Scalability: Choose connectors that support future upgrades or platform variations. For example, a 2-cavity connector for an EV sensor should be compatible with both 12V and 48V systems to accommodate evolving architectures. Modular designs also simplify repairs and replacements, enhancing project longevity.
Evaluate supplier reliability and availability. Major manufacturers like Molex and Aptiv offer global supply chains, ensuring consistent availability for large-scale projects. For prototyping, consider distributors like DigiKey or Mouser, which provide small quantities for testing.
Step 5: Align with Industry Trends and Standards
To future-proof your project, align the connector choice with automotive and industrial trends:
- Electrification: As EVs adopt 48V and 800V architectures, select 2-cavity connectors with sufficient current capacity and insulation for auxiliary systems like cooling or BMS. For example, TE’s Power Double Lock connectors support moderate-power EV applications.
- Autonomous Driving: ADAS requires connectors for sensors and data networks. 2-cavity connectors used in radar or camera modules must support high-speed protocols (e.g., LIN or CAN) and EMI shielding to ensure signal integrity.
- Connectivity: With vehicle-to-everything (V2X) and 5G integration, connectors must handle low-latency data. 2-cavity connectors for communication modules should prioritize gold-plated terminals and compact designs for space-constrained dashboards.
- Sustainability: Choose connectors with recyclable materials or modular designs to align with circular economy principles. Durable connectors reduce replacement needs, minimizing waste.
Ensure compliance with standards like ISO 16750 (environmental testing), SAE J2030 (sealing), or USCAR (performance). These standards guarantee reliability and interoperability, critical for automotive and industrial applications. For example, a connector for an EV project should meet ISO 17409 for high-voltage safety.
Step 6: Test and Validate
Before finalizing the connector choice, conduct thorough testing to validate performance:
- Prototype Testing: Build a prototype with the selected connector to verify electrical performance, mating reliability, and environmental resistance. For example, test a sealed connector in a simulated under-hood environment with heat, vibration, and moisture.
- Compatibility Testing: Ensure the connector integrates seamlessly with existing systems, such as wiring harnesses or mating components. Verify wire gauge compatibility and locking strength.
- Stress Testing: Subject the connector to extreme conditions (e.g., thermal cycling, vibration, or salt spray) to confirm durability. Use standards like ISO 16750 to guide testing protocols.
- Supplier Support: Leverage manufacturer resources, such as technical datasheets or application engineering support, to address any issues during testing.
Iterate based on test results, adjusting the connector choice if needed. For example, if a connector fails vibration testing, consider a design with a stronger locking mechanism.
Conclusion
Choosing a suitable 2-cavity connector for a project requires a systematic approach, balancing technical requirements, environmental demands, and cost considerations. By defining project needs, evaluating design features, matching connectors to applications, and aligning with industry trends, engineers can select connectors that ensure reliability and efficiency. 2-cavity connectors, with their compact size and versatility, are ideal for a range of applications, from automotive sensors to industrial automation. Their ability to support power, signal, and data transmission in harsh environments makes them a critical component in modern projects. By testing and validating the chosen connector, you can mitigate risks and ensure long-term performance. As the automotive and industrial sectors embrace electrification, autonomy, and connectivity, selecting the right 2-cavity connector not only addresses immediate project needs but also positions your design for future scalability and innovation.
For more about the best automotive electrical connector manufacturers and suppliers in thailand, you can pay a visit to Gvtong at https://www.gvtong.net/ for more info.
Recent Posts
How Many Tips Do You Know About De-Pinning and Re-Pinning Connectors
Application of Electrical Connectors in Powered Autonomous Vehicles
How to Choose the Right Seal for Your Vehicle Wiring Connections
Made in China: Benefits of Domestic Electrical Connectors
Tips for Selecting Heat-Resistant Wiring in Vehicle Hot Spots
Detecting & Fixing Loose or Faulty Connections in Car Wiring
How Does a Qualified Mechanic Solve Car Electrical Problems?
Tags
Recommended Products
-
GB Series-Energy Storage Connector-10.0mm
-
Low voltage connector-20PIN socket + plug
-
GH800 Series-3-core plastic high voltage connector
-
Signal connector – waterproof, three-row, 8-pin
-
GHDC terminal
-
GIPT 2-core wiring connector
-
Automotive FAKRA Single Head Connector, Automotive Standard FAKRA Connectors
-
GH Series-DCDC Through-the-Wall Terminal B